By Bjorn Dahle, KIC
The majority of today’s SMT market today in the United States and Europe is high-mix/low- to medium-volume and parts of it even are considered extreme high-mix and/or extreme low-volume. In the US market there is talk of high-mix/higher volume while increasing efficiency. Many production lines now experience more downtime than production time. Production downtime is the result of numerous factors, but mainly it is caused by machine setup and changeover time. One critical machine that can contribute to much of the downtime or potential success of a production line is the reflow oven. The oven can be very time consuming to set up for a new PCB assembly, and often it is the slowest machine in the line changeover. This can significantly – and negatively – affect profit and delivery times. There have been many technologies developed for the mass production factories of China and other lower cost countries. Less attention has been focused on the unique needs and technical solutions of high-mix markets.
SMT assemblers strive to produce strong solder joints without damaging components or substrates during the soldering process. Solder paste, substrate and component manufacturers provide tolerances or process windows that need to be followed. The best manufacturing practice to manage the reflow process is to attach thermocouples (TCs) to every unique PCB part number and select an oven setup that positions the PCB profile in spec. In-spec is determined by measuring a time vs. temperature profile that conforms to the interface between multiple process windows:
• Solder paste specification (or other material like underfill)
• All relevant electronic components’ tolerances
• Design challenges reducing the process window such as large mass heatsink BGAs next to small mass components like 0201s or smaller
• Substrate data and tolerances
Laminate TG and Td, layer counts, copper weights, HDI or non-HDI, etc.
Surface protectant: OSPs are becoming more complex, requiring specific temperatures for assembly in order to survive multiple reflows and cleaning, while attempting to achieve optimal efficiency
Jose del Valle, industry expert and COO/Vice President of NuVal EMS, a high-mix contract electronics manufacturing company based in California, believes that it is not sufficient to process most components within spec – they ALL have to be processed in accordance with the relevant process window. He said that this can prove difficult, however, since there may be hundreds or even thousands of components being soldered to the same substrate, and the position on the substrate along with the thermal mass will influence how they heat up and cool down. Additionally, the components may have process windows that differ from each other.
Many factories will assemble dozens and even hundreds of unique assemblies monthly. While some of them – like NuVal EMS – can and will run their thermal process the “correct” way, others cannot or will not for various reasons: no representative production PCB is available for profiling; process window information for some components is lacking; limited time or resources available to profile each unique PCB; oven changeover/downtime is deemed to be too long.
So what happens if a factory cannot use best manufacturing practices for the reflow process? There are technologies and methods available that can help them come close.
At the fundamental level, an electronics manufacturer is in the business of producing products at the quality requested, delivered at the agreed upon schedule, at a price the customer is willing to pay, and at a cost that allows the manufacturer to be successful. Everything else is a means to an end. Profiling, traceability, process control, inspection, and more are not an end in themselves (unless a client specifically requests them), rather they are tools to be used to improve quality, productivity and cost reduction in order to help the manufacturer become successful.
To help manufacturers become more successful, software that recommends the best oven setup for each assembly to produce an in-spec profile is available today from several companies, such as KIC’s Navigator. The software can handle different process windows for different components on the same PCB, and it dramatically reduces oven setup time. However, it does require that a minimum of one profile is run first, and therein lies the rub. Until recently I did not quite appreciate the difficulty some factories have in acquiring a relevant PCB for profiling, or to take the time to follow best manufacturing practices. EMS companies, for example, are frequently provided X number of boards and are supposed to provide X number of assemblies, not X minus a profiling board or two.
Some oven setup tools are designed to help factories that cannot always use best manufacturing practices for their reflow processes. Various elements of Auto-Focus include:
Technology to reduce the need to profile
A very exciting technology that promises to greatly reduce setup time is oven setup software that utilizes a built-in database that does not require an initial profile run even for a new PCB assembly. The technician simply inputs the length, width and weight of the PCB, and the system recommends the best oven recipe in a few seconds — without running a profile. Whether the technician decides to run a verification profile afterwards (recommended) or not, this more scientific method at least offers improvements over the common “guessing game” going on in factories every day — namely looking at a new PCB assembly and using the oven settings currently employed for the most similar PCB, while not even running a profile afterwards.
The software automatically recommends the oven set up that uses the least amount of electricity – without running a profile, simply by entering the product length, width and weight into the software. Such easy-to-use products enable technicians to achieve expert process results.
Additional technologies offer near instant oven changeover. To explain how they work, let us first look at the challenge at hand. An average reflow oven has literally billions of alternative recipes because each zone temperature can be adjusted in small increments within a wide range. Additionally, the conveyor speed adds yet another variable to form a huge number of possible combinations. The oven setup software will perform an exhaustive search of all of them, and for each unique oven recipe it will predict the profile and its relationship to the relevant process window. (This prediction task takes only a few seconds after an initial profile is run.)
Avoid oven changeover by identifying a common recipe for several different PCB assemblies
Prediction software can be used to identify a common recipe that can process groups of different PCBs. One method is to simply attach a large and a small PCB to the same profiler. The software will search for a recipe that can process both PCBs in spec, therefore the other PCBs in between will be in spec. Depending on the oven capability, it may not be possible to use a single common recipe for all PCBs. Instead, the software can generate a select few recipes for groups of small, medium and large PCBs. As always, running a real verification profile with TCs attached to the PCB is recommended, but frequently omitted.
Eliminate waiting time for oven to stabilize on new temperatures
Another application of prediction software is that it can identify a new oven recipe by only changing the conveyor speed, and keeping the zone temperatures the same. Oven changeover from one recipe to another using the same zone temperatures with a different conveyor speed is near instantaneous. On the other hand, a reflow oven may need up to 30-45 minutes to stabilize on a new recipe if the new temperatures differ greatly from the current. This is especially true when the oven changes from a hot to a cooler recipe. Some SMT factories like Nu-Val EMS have long realized that a reflow oven will heat up much faster than it cools down, and the production manager will schedule the day’s batch of production runs by starting with the coolest oven recipe and ending with the hottest. This approach requires more pre-production planning across the organization, but enables a higher mix environment to become higher volume by improving efficiency, added del Valle.
Automate profiling
Some companies, especially automotive and other high-reliability electronics, demand best manufacturing practices. The manufacturer will have no choice but to set up the oven correctly and run verification profiles. Discussions between manufacturer and clients take place constantly in regards to the frequency of profiling. One camp states that reflow ovens are so stable that profiling can be performed less frequently. The other camp argues that running verification profiles even as frequently as every shift means that production is running blind that whole shift. Common variations like changes in the exhaust system, thermal loading, pressure changes, and human errors may affect the thermal process significantly. Automatic and continuous profiling that measures the profile in real-time for each and every PCB being produced is becoming popular among many manufacturers because the technology provides traceability, eliminates the problem of running blind in between spot checks, and eliminates the production downtime associated with periodic manual profiling. The systems will further reduce downtime by monitoring the oven during the changeover phase and alert the technician the moment that the oven is ready for production. Another source of downtime can be the time it takes to troubleshoot a production run that has stopped due to a yield problem. Although typically less than 5-10 percent of defects are attributed to the reflow process, many factories will run a profile to troubleshoot the yield issue. This is due to the lack of process information in this historically “black box” reflow oven. Automatic profiling will inform the engineer immediately whether the problem is in the reflow process or not, reducing troubleshooting time. If the problem is in the thermal process, the system provides information to identify the problems in the oven.
Conclusion
It is not uncommon for production lines at SMT factories to spend more time on setup and line changeover than actually running production. Additionally, following best manufacturing practices for the reflow process may not be possible or acceptable at these factories. Today, process engineers and managers are doing their best with what they have. They can use techniques like scheduling the production batches to run cooler oven recipes in the morning and progress towards hotter recipes at the end of the day.
To significantly improve profitability, however, high-mix/low-volume manufacturers are taking advantage of new technologies such as prediction software. Oven setup and process optimization software may improve both productivity and quality by allowing for a more scientific and accurate approach to reflowing the assemblies under such difficult circumstances.
NuVal EMS achieves high yields and low costs by ensuring that every product it makes is well designed, properly laid out and in concert with the client, and thoroughly tested before going into production. Customer service and personalized solutions also are extremely important to NuVal EMS, so the company focuses on providing customers with the highest possible levels of quality and productivity. “There are hundreds of contract manufacturers to choose from, but there are very few that do what we do: focus exclusively on the customer,” said del Valle. “At NuVal EMS, we don’t want to just churn out products for clients we may never see again. Our focus is on developing long-standing relationships with clients where we become an extension of the client’s engineering and operations team. We want to take on customers’ most difficult challenges and turn their product sketches into trailblazing innovations.” To find out more about NuVal EMS Inc., contact Jose del Valle, COO/Vice President at 14831 Myford Rd., Tustin, CA 92780; 714-544-0105; E-mail: ; Web site: www.nuval-ems.com.
For more information, contact Bjorn Dahle, President, at KIC, 16120 Bernardo Center Dr., San Diego, CA 92127; 858-673-6050; E-mail: ; Web site: www.kicthermal.com.
Skyscraper 1
Skyscraper 2
Skyscraper 3
Skyscraper 4
Skyscraper 5
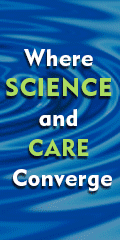