Since its foundation in 1976, SEHO has become the worldwide contact partner whenever soldering is involved. Today, SEHO is a globally leading manufacturer of complete solutions for soldering processes and automated production lines. Company solutions are based on performance, flexibility, efficiency and technical progress. SEHO’s business activities and production organization are oriented according to the principles of sustained future-compatible development. With its systems, the company provides customers with a sustained and resource economizing production facility. It continuously develops its technology in order to provide customers with a competitive advantage.
Markus, since the company’s founding almost 40 years ago, SEHO has pioneered numerous innovations in the field of soldering, such as soldering in Nitrogen atmospheres and soldering processes for high temperature applications. Tell us about some of the company’s more recent developments.
Due to continuous investment in research, cooperation with industry and science partners, and our highly motivated team, we are able to quickly react to new trends in electronics manufacturing and convert them into processes and products for serial production.
Innovations from SEHO focus on one point: to increase productivity. This includes both the reduction of downtimes for machine setup and maintenance, and the increase of production quality. The overall goal is a defect-free production process.
The demands of current and future assemblies regarding a suitable joining technology require new concepts. For example, to activate the surface of the printed circuit board (PCB) prior to wave soldering, a solvent-based flux typically is used. One of our most recent developments is a plasma process that can be used to deposit flux powder, which eliminates the need for a solvent. The powder (e.g., Adipic acid) is firmly applied to the PCB’s surface and offers long-term stability. The soldering result with a standard fluxing process is identical. This new plasma process reduces creep when using masks as well as reduces residues, remarkably improving both product quality and system downtime. Additionally, eliminating the solvents allows for material cost savings.
Voids in solder joints are nearly inevitable for common process conditions. How can SEHO help reduce voids in reflow soldering?
Whether for power electronics, electronic aviation systems, medical equipment or electronic systems for the automotive industry, solder joint voids represent a significant problem. Enclosed voids can cause a displacement of electrical and thermal paths as well as local concentration of power and heat.
SEHO’s MaxiReflow HP offers innovative technology that ideally combines convection heat with a special hyper-pneumatic module, thus ensuring virtually void-free connections. Instead of using a complicated vacuum process, MaxiReflow HP is equipped with an effective excess pressure chamber, allowing shorter cycle times and enabling gas convection to be used for heating assemblies. Additionally, solder balls that can be seen in vacuum processes are effectively avoided with this technology.
Each heating zone of the MaxiReflow HP – also the zones integrated in the hyper-pneumatic chamber – has a tangential fan that ensures absolute homogeneous heat distribution with the large volume of ventilated process gas. This enables the most effective and component-sensitive heating of the products with set temperatures on a low level.
The process is designed in such a way that the solder alloy has been molten before entering the first section of the hyper-pneumatic chamber. In the second section of the hyper-pneumatic chamber, the solder can solidify in an excess pressure environment. This innovative concept makes existing voids finally vanish from the solder connections. Immediately after the solder’s solidification, the excess pressure is released and the assembly is delivered to the cooling zone.
When processing uncritical assemblies, the MaxiReflow HP also can be operated without activating the hyper-pneumatic chamber. In this case, the PCBs go through a conventional reflow soldering process.
It appears that today’s production faces frequent new challenges with numerous component variants and fluctuations. How does SEHO help solve these challenges?
The SEHO LeanSelect is particularly designed to meet these challenges, featuring highest flexibility and outstanding return of investment. While the entire process is fully automated, loading and unloading of assemblies is done manually on two separate conveyors. This allows simultaneous processing of up to five carriers.
The work stations are arranged in a counterclockwise U-shape, thus consistently following the Lean Equipment Design Guidelines. The fluxer and soldering unit are mounted on the same high-precision axis system to ensure highest energy efficiency and successively approach the solder joints, while the assemblies remain in a fixed position.
Depending on the application, the LeanSelect can be used for both flexible mini-wave processes and product-specific dip soldering processes with high throughput. Quickly exchangeable solder nozzles and multi-nozzle tools ensure short changeover times. The LeanSelect ensures the highest productivity in the smallest footprint, with the same uncompromisingly high soldering quality as the high-end systems from SEHO.
With selective soldering systems from SEHO, electronics manufacturers are one step closer to a zero-fault production. They all provide a comprehensive, innovative hardware and software package to control the process sequence 100 percent, which is absolutely unique. Additionally, selective soldering processes can be traced completely. With our software feature mcServer, selective soldering systems from SEHO are ready for Industry 4.0. mcServer allows comprehensive control of the soldering process with real-time access to all connected machines that are installed in different production sites worldwide.
We have read about SEHO’s SelectLine in the news lately. Can you briefly explain what this system is and why it has met with so much global acclaim?
Time plays a key role in modern electronics production. The SelectLine machine concept is consistently modular, thus ensuring quick reaction to changing production volumes and providing clear cost benefits. Additional fluxer, preheat and soldering modules can be integrated – even at a later date – to respond to higher complexity of board layouts or increasing throughput requirements. The soldering area of the SelectLine scores highly due to its outstanding precision and flexibility. Two electromagnetic soldering units for mini-wave or dip soldering processes may be integrated.
The technological highlight of the SelectLine is the patented Synchro concept, an intelligent software feature that doubles the production volume. Therefore, costly dual conveyor systems are not necessary.
Maximum machine availability is ensured with the automatic ultrasonic cleaning for mini-wave solder nozzles that is patented by SEHO. What previously had to be made manually and with aggressive chemicals, now is environmentally friendly and automatically performed through the machine: the solder nozzles get a gentle cleaning and they are completely wetted.
Besides significant time savings in terms of maintenance, this feature provides an absolutely stable soldering process. Both the LeanSelect and the SelectLine can be equipped with this new feature.
Besides the technical solutions you offer, how can end-users profit from working with SEHO?
With our modern and innovative machines, and the high quality standard of our products, we are a strong and reliable partner for our customers worldwide. Moreover, our customers profit from complete solutions, a strategy that we have consistently implemented over the last few years. SEHO is the only manufacturer worldwide that provides innovative systems for all fields of automated soldering processes with integrated solutions for automated optical solder joint inspection.
This strategy also includes customized automation of complete production lines for board handling and material management, particularly in through-hole processes. Work places for assembly of electronic components, buffer and paternoster stations, turn stations, automatic lifts and, of course, the completely automated conveyor units in between are only a few examples. Moreover we implement manual, semiautomatic and automatic work places for the final assembly of products and subsequent testing procedures, either in individual production islands according to Lean Production guidelines or in interconnection with the entire production process. Our engineers focus on improvements in the workflow, thus reducing manufacturing costs. SEHO assists customers with creative ideas during planning and construction, and we also manufacture, assemble and install the production line.
In the center of our attention are the employees working at the manufacturing line. We provide ergonomic, individually height-adjustable workplaces and the automatic adaption of connected handling stations as a matter of course.
Finally, customers profit from SEHO’s outstanding knowledge and experience that we provide in various seminars and individual trainings from the SEHO Academy.
What are the current trends in soldering and how does SEHO manage to keep up with the ever-changing industry?
The globalization of markets results in stronger competition with considerable cost pressure. Therefore, the ability to reduce manufacturing costs in electronics production while maintaining a consistent high product quality is essential. The clear objective is a stable and reliable zero-fault production.
At productronica 2015 in Munich, SEHO will introduce such a zero-fault production line for selective soldering of through-hole components that are “automatically” free from defects and completely traced. Besides the selective mini-wave soldering process, this production line incorporates an AOI system that is integrated in the selective soldering machine, a verify work station for verification and classification of detected faults as well as an automated rework soldering process. Intelligent handling units automatically allocate the assemblies to the next individual work station or buffer them until the following work station is ready to receive a board.
Because of the creative handling concept, this zero-fault production line provides shortest cycle times and small floor space requirements.
All processes are independent from the operator and fully reproducible. Additionally, the entire board will not be reprocessed, only verified defects are repeatedly processed with correspondingly adapted parameters. These features, as well as the ability to completely trace all processes throughout the line, are only a few of the outstanding advantages of this zero-fault production line.
SEHO will continue to work closely with customers, industry and science partners to research new technologies, and integrate innovations for the development of new products to further improve production processes. Our particular strength lies in our innovative spirit and support, bringing our customers the next step in optimizing their profitability and competitiveness.
Skyscraper 1
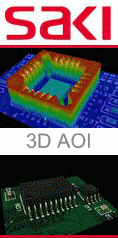