Patrick McWiggin, SolderStar’s Technical Director
With today’s more sophisticated electronics market, which calls for more intricate and diverse requirements, together with decreased development cycles and improved capacity, the need to ensure products are produced correctly with the right process control and within tight constraints is ever more important.
To guarantee products are soldered correctly and process parameters are met, thermal management is a necessity. To produce electronic assemblies without a known thermal profile is detrimental, as you ‘cannot manage what you do not measure’. Without correct profile management, increases in rework costs may occur and potentially give rise to early field failures. There are three levels of process control which are commonly employed today, all with differing benefits and failures starting with the traditional test board method, through to the advanced automatic profiling systems. Over the years thermal profiling has advanced significantly and now offers exact profiles aiding in the advancement of technology manufacture. We will first look at the traditional manual method.
Traditional profiling devices – how this method is no longer the preferred choice for production line verification profiles
The method of passing a profiling device through an oven to ensure the machine is set correctly is an important one, and having a test board to do the initial profile setup is still a fundamental step that needs to be performed. Thermocouples are placed on the crucial components of the board and when passed through the oven measurements are taken to ensure the thermal profile meets the target profile.
With the introduction of more complex or smaller fragile assemblies, or when high production volumes of mobile phones and tablet PCs are involved, this is simply not enough. Verification of the oven profile must be performed much more frequently. Using the test board for on-going process checking is error prone, resulting in false alarms or measurement data with poor repeatability or accuracy.
The main problem with this method is keeping the test board in good working order. The thermocouple sensors used to establish the profile during the initial set-up stage needs to respond quickly to temperature change and not influence the measurement. The result of this is that they are inherently fragile and need to be frequently replaced which is both time consuming and can result in measurement repeatability problems. Attachment of the sensors can also be difficult; they can be placed incorrectly on the board, fall off or get snagged in the machine. Together with the problem of repeated test runs damaging a PCB, resulting in an inaccurate measurement, the drawbacks to this method are great.
Man hours is another drawback to the manual method. The process interrupts production and is very labour intensive. It is also very dependent on an individual’s expertise to attach the thermocouple sensors correctly and in the right place. Capturing the true profile, then the ‘golden standard’, which is imperative to the product working correctly, is not easily achieved.
Oven Verification devices – add-on technology to capture the Golden Standard
Because of these drawbacks to using traditional thermal profiling devices, combined with test cards, companies like SolderStar, worked on devising technologies that would give ease the process of capturing oven verification profiles. There was a need for a device that monitored oven temperatures effectively, without putting constraints on the machine, and the technicians working them. There was also the need for software that documented the profile accurately and could be easily traceable. This is especially important today with government regulations and original equipment manufacturers imposing higher standards. The medical and automotive industries are just two industries that have pushed demand for more critical control and traceability, therefore oven verification devices were born.
One example of this technology is SolderStar’s DeltaProbe. This product was designed and developed to combat the problems of traditional manual profiling and gives manufacturers a more streamlined method for periodic profile. The DeltaProbe offers a process control and intelligence that matches manufacturers more intricate and detailed production requirements, without the need to use fragile test boards for daily oven checks.
The DeltaProbe was designed to use the unique SolderStar ‘Smart link interface’, this makes for an intelligent fixture which can hold product and process recipe information to allow efficient profile capture, download and organisation. Smart link provides the secondary function of a quick connection system eliminating the possibility of channel mix-up error.
Oven verification devices like the DeltaProbe include specially designed measurement sensors where all process records are captured without a test card or wires getting in the way of the procedure. This makes it not only robust, but the appropriate tool to generate highly repeatable results, an important requirement today, which stands up to regulatory requirements.
By using an oven verification tool, a ‘golden’ process profile can be measured easily and tolerance limits can be set around the temperature traces and process parameters. This ensures measurements are precise and any oven performance changes or problems are quickly flagged and remedial action can be taken. This makes periodic testing of the oven more repeatable, convenient and user-friendly, resulting in better process documentation at a lower cost to the manufacturer.
Platforms like DeltaProbe far outweigh test card methods for a number of reasons;
- The usual use of test cards need constant maintenance and it is not easily repeatable. This results in false errors due to measurement platform problems.
- Statistical Process Control (SPC) gathering is easy and offers a more accurate measurement.
- Matched sensors show any performance problems across the width of the oven heater.
- There are independent limit settings per oven zone which gives more control in critical zones.
- A number of errors can be detected easily including speed, conveyor and recipe loading and editing errors.
- It can be used to capture a benchmark for multiple of lines – a must for high production volumes
All these benefits help to give a true picture of the process capability and result in higher quality soldering within the end product. Platforms like this can be used once a temperature profile is captured from a real test PCB. The ongoing process monitoring will then be achieved by measuring the difference from an established process baseline. The software used with such products also includes advanced SPC tools which create charts for ongoing process control measurement, trend evaluation and corrective action. This process, as you can see, far outshines traditional profiling methods.
Continuous Oven Monitoring – How can we outperform the periodic profiling technology of today?
Safety critical or high value assemblies, combined with tighter processing constraints, and the need for complete process documentation has driven the development of profiling systems that can monitor every electronic assembly produced on the manufacturing line. The pinnacle of profiling systems today are those that can record and provide traceability of the process conditions within the oven for every electronic assembly. For this reason the SolderStar APS (Automatic Profiling Systems) was developed.
Platforms like the SolderStar APS measure the stability of the process parameters within a thermal process, combined with assembly position tracking, to produce the most representative virtual profile possible for every PCB passing through the machine. Such platforms can continuously track PCB movements through the machine and monitor process fluctuations at product level. These changes are then used by a mathematical model to calculate what the resulting PCB profile or ‘virtual profile’ would be. These process parameters can then be calculated and tested within limits.
The APS uses a novel technique to reduce the number of thermocouple conductors required to make the product level measurements needed, allowing for a much smaller probe diameter to be achieved. For example on a 14 zone machine a probe diameter of typically 6mm could be used. This results in robust yet fast response probe design essential for achieving the detection of machine faults quickly and easily so they can be rectified, saving both time and money.
Faults that can be detected on APS platforms include checking if the zone temperatures and speed are set incorrectly from a defined reference, rapid feedback on thermocouple and conveyor and fan failures. Also the oven recipes are monitored to finally ensure they are inputted correctly and there is no overloading of the oven.
SolderStar APS can continuously compare each new set of measurements with the reference and evaluate any differences. If the difference between the current process and the reference exceed user defined limits, then further boards are prevented from entering the oven by way of the SMEMA (Surface Mount Equipment Manufacturer’s Association) interface.
Special temperature probes are mounted along the heated length on both sides of the machine to monitor actual product level temperatures in real time. In addition to this, the system keeps track of the current speed and position of each assembly in the process.
The temperature probes have been designed to be smaller, and can be positioned closer to the PCB providing a much more accurate temperature measurement in the vicinity of the electronic assembly during soldering. The smaller size also reduces the danger of the probe shadowing the product. Such a system also measures the product level zone temperatures and conveyor speed independently of the oven stopping the machine from malfunctioning if for example, a heater or fan is ineffective, or an operator error loading the wrong recipe for the board being produced.
The continuous nature of the APS means that the thermal process no longer runs blind. The profile for every single PCB is modelled and verified to meets the requirements of that particular assembly. It is also designed specifically to meet the strict requirements of the manufacturer lowering the cost of production by reducing production downtime due to rework and labour. The age old problem of ‘you can’t manage what you can’t measure’ is no longer a problem with this state-of-the-art profiling technology.
All these benefits have improved manufacture and saved in time and money as it is a permanent and immediate method of profiling. Because of these obvious advantages manufacturers of military, automotive and medical devices are moving towards this technology as their preferred method of profiling as it is consistent, accurate and provides 100% traceability through advanced software.
In a nutshell the APS system can discover ‘problems’ as they happen which can be rectified easily and efficiently reducing down-time and man hours and is a fail safe way to ensure that PCB assembly and manufacture is correct with guaranteed traceability.
Skyscraper 1
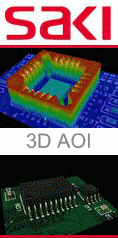