ULT AG has further developed its extraction and filtration system for removal of laser fume and laser dust, the LAS 2500. The system is based on an ideally configured device and filter concept that provides users with high contaminant filtration rates, simplified filter handling and long filter lives. In addition to cost and time savings, users benefit in reduced compressed air consumption, resulting in lower energy expenses for jet or rotary nozzle dedusting of the applied filter cartridges.
The LAS 2500 extraction system was developed for removal of laser fumes as well as dry non-flammable dusts. It is ideally suited for utilization in laser material processing, e.g. laser cutting, laser welding, laser structuring, laser marking or laser ablation. The extraction and filtration system was designed for applications that generate larger amounts of airborne pollutants.
The LAS 2500 benefits from the utilisation of conic filter cartridges, thereby enabling increased filter performance and pressure, and independent pneumatic cleaning due to the filter cartridge’s design layout. These high quality filter units are dust grade M compliant with DIN EN 60335-2-69:2008e, ensuring high separation efficiency for various particulate matters of more than 99.99 %.
An optional swing check valve protects pipelines against pollution by possible dirt pushback, and consequently, filter cartridges against premature wear. An additional benefit is the easy disposal of low contaminated dust deposits that are collected directly into a 70 l removable container.
Because of its small footprint, the extraction and filtration system LAS 2500 can be flexibly adapted to various process conditions, particularly in limited spaces, and therefore, helps to save valuable space on the production floor. This optimised efficiency is characterised by front access to the system and the opportunity to select the extraction position, i.e. raw gas intakes can be located on the system’s right or left side.
Due to a high filtration rate, purified air can be recirculated to the working area avoiding heat loss.
Additional information on ULT and its products can be found online at www.ult.de.
Skyscraper 1
Skyscraper 2
Skyscraper 3
Skyscraper 4
Skyscraper 5
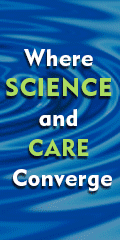