By Steve Heinzen, NEO Tech VP Strategy & Marketing
North American OEMs considering the best electronics supply chain solution for their businesses have many options. As product lifecycles shrink the importance of architecting a highly responsive supply chain increases. Succeeding in the design of the best fitting supply chain to their needs requires companies to answer questions such as
What is my product lifecycle? And how much business flexibility to I need?
Should we insource or outsource?
What location (off-shore, near-shore, on-shore) provides optimal balance of cost, risk, speed and flexibility?
There is no single answer that fits every scenario, but some trends have certainly shifted the balance for those making moderate to high complexity products sold into the North American Industrial and Medical market sectors. Ten years ago, more frequently than not, the de-facto answer for most OEMs was that they needed to build electronic products in Asia to be globally competitive. Since then China in particular has experienced significant labor cost and wage inflation in the manufacturing sector and continues an upwards wage trajectory faster than most competing markets.
Nearshore manufacturing options today offer a practical alternative for controlling costs and minimizing supply chain risks for OEMs. The goal should be the lowest total landed cost that achieves the required business flexibility.
Evaluate Supply Chain Options Using Total Landed Cost (TLC)
To determine the best nearshore market for an individual company’s needs, it is important to run an optimization model that determines the lowest total landed cost based on labor, material, transport and regulatory costs. That includes the cost of the product, which is comprised of labor, materials and overhead, plus all the shipping, freight, duties and taxes. Companies also need to take into account that fuel prices and security concerns can drive up logistics costs. As part of the optimization model, OEMs should consider not only the quoted TLC, but the likely impact of schedule variation and premium freight used to avoid inevitable supply disruptions.
As the labor costs in China rise relative to Mexico, the landed cost into the US market for many products – makes Mexico a better value. The proximity of Mexico to the United States and Canada is especially advantageous in reducing logistics cost and transit times.
Consider the “Soft Costs”
Nearshoring offers companies many advantages. Less often considered is the comparative ease of doing business in the same or near time zone, with the supply partner that can conduct business in English, with many culture similarities vs. alternatives such as China, Malaysia or India. Company’s employee quality of life is better when they can have conference calls with the nearshore manufacturing partner during regular work hours, as opposed to late into the evening, often at home, when the Asia supply base starts work. Trips to the factories, especially in Mexico border locations can be made day trips – not week long trips when traveling to Asia. Employees can spend more productive time doing value added work and use nights and weekends to achieve a healthier work/life balance.
Mexico nearshore solutions provide access to low-cost labor, and border-based manufacturing facilities that offer logistics simplicity, proximity, language while cultural closeness to the US market enables good grades on ease of doing business.
NEO Tech as a Nearshore Partner
NEO Tech operates 14 manufacturing locations across the U.S. Mexico and China. NEO Tech’s Otay Mesa site located in Tijuana Mexico and Agave site located in Juarez Mexico both deliver nearshore solutions and offer close proximity to US logistics hubs – both just a few miles from the U.S. border. The NEO Tech engineering, supply chain and operations specialists work closely with current and prospective customers to evaluate their project needs and architect solution options that best align to each Company’s objectives.
To make nearshoring successful, companies must choose the right partner: one who has experience navigating the ins and outs of nearshoring as well as sharing the goal of manufacturing quality products in the most cost-effective manner. Below are examples of NEO Tech successfully implementing nearshore solutions in its Otay Mesa and Agave sites for key customers.
Customer Solution Example “Company A”
A medical device leader in patient monitoring products sought help from NEO Tech to return their electronics manufacturing to nearshore after an onerous Asia experience. A technology leader in hospital patient monitoring solutions had sourced their PCBA with a large Tier 1 EMS with manufacturing in Malaysia. The products were complex and required an enhanced PCBA-level functional test – well beyond simple validation of manufacturing workmanship – to ensure the products met the Company A’s unique and safety-critical requirements. The long distance supply chain caused frequent business disruptions for the Company A when faced with NPI launches, ECO implementation and even minor quality problems.
NEO Tech proposed a nearshore solution at its Otay Mesa site, with its location just across the Mexico border and just a few hour drive from the Company A’s development location. Being in the same time zone enabled the Company A team members to conduct calls with their EMS counterparts during business hours instead of interrupting family time with calls that extend into the evening. Company A visits to the manufacturing site were day trips instead of expensive, time consuming weeklong trips and 15+ hour flights. Additionally, outbound logistics and transit time from NEO Tech to the box build location became one day vs. many weeks, reducing logistics costs and needed inventories to buffer disruptions. Finally, NEO Tech’s test development team created a dedicated test rack system capable of achieving the Company A’s test requirements and also a unique advanced test fixture design that has the needed capability to substantially increase the test measurement precision well beyond what was previously available on the market.
The NEO Tech Otay Mesa Nearshore solution offers similar landed cost vs. the previous Asia solution. But, today, Company A experiences fewer disruptions in supply, faster time to market with newer products, and a better work environment for Company A employees managing the EMS supply base. Additionally, they have benefited from having a test development partner they can rely upon to extend the reach of their internal product development organization.
Customer Solution Example “Company B”
Company B is an American OEM of backup power products for residential and industrial markets needed improved time-to-market as well as a competitive and flexible manufacturing solution. NEO Tech’s Agave site provided the solution. Previously, Company B used an Asian EMS to produce their wireless remote monitoring and control devices. The extended supply chain distance from the key market in the US caused issues with flexibility and service levels. A next-generation redesign upgrade also was behind schedule.
NEO Tech proposed a solution that combined both engineering services to assist the customer finalize a new design revision to the wireless interface and a nearshore manufacturing solution in the NEO Tech Agave site in Mexico. NEO Tech initially conducted a DFM review on the new product. Then prototypes of an improved design were built with additional VA/VE recommendations to validate the needed changes – and delivered only 10 days after receipt of the initial design PO. Additionally, NEO Tech collaborated with an industrial design partner to rapidly produce mechanical samples and enable the completion of the design, and help get the program schedule back on track. The Agave final production location enabled significantly more flexibility and increased service levels with its close proximity to the US market.
Company B found that using an EMS partner that can closely collaborate with their US-based engineering team and can help them execute rapid design cycles with quick turn PCBA and mechanical sampling capabilities accelerates their time to market. Additionally, having a close connection to a nearshore manufacturing solution provides a compelling fit to their business.
Customer Solution Example “Company C”
Company C is a large, diverse North American laboratory equipment OEM that was seeking help consolidating PCBA supply across its divisions. NEO Tech’s Otay Mesa manufacturing facility helped the company increase flexibility and cost savings. Company C originally had numerous US-based production locations that all needed low-volume/high-mix PCBA suppliers, with each location managing their own local sourcing – mostly at small local EMS companies. They faced frequent obsolescence-related supply disruptions because their products had very long product lifecycles. Also, some of their products were technically complex to build, sometimes beyond the processing skill of the small tier EMS providers.
NEO Tech’s solution was to consolidate the PCBA business from eight customer divisions into the NEO Tech Otay Mesa site, with over 250 active assemblies. Later, it was expanded to include 12 different product divisions. Extensive engineering and supply chain actions were taken to mitigate obsolescence issues with identification and focus on “at risk” parts and increase materials availability by increased use of distribution VMI. Additionally, NEO Tech moved more than half of the products to a demand pull fulfillment model to increase flexibility. Also, sourcing support was offered to migrate the customer AVL to NEO Tech preferred suppliers, which decreased materials costs. Finally, NEO Tech expanded value further by adding the manufacture of higher level subassemblies and box build. A unique NEO Tech transfer process was used that reduced transfer risk with an onboarding “pull” team ensuring tribal knowledge was documented and transferred seamlessly to the customer.
Today, Company C is enjoying improved on-time delivery performance and flexibility with a much more competitive cost model vs. the prior solution. The nearshore solution at NEO Tech Otay Mesa provided the best combination of competitive costs with business flexibility, and with much lower soft costs associated with managing an outsourced supply chain versus going to Asia.
Lessons Learned
Based on these real customer examples NEO Tech confirmed several hypotheses. Companies can achieve globally competitive cost structures for their medical and industrial electronic products with nearshore solutions with the additional benefits of having increased flexibility and lower risks. Nearshoring has demonstrated favorable impact on the speed of launching new products, especially when offered through an EMS partner with strong product realization services to support Companies’ product development and engineering activities.
Conclusion
Asia sourcing for many medical and industrial for products destined for North American markets is losing favor rapidly amongst Companies for many reasons including rising labor and transportation costs, painful disruptions due to lengthy supply chains, and lack of IP security. Additionally, for many, manufacturing in China and other offshore locations is neither cost-effective nor flexible. Instead, manufacturers are bringing production closer to home. Nearshoring is today’s solution because it allows companies to reduce supply chain risk while streamlining operating costs. Additionally when you choose the right full service product realization partner with cost effective nearshore locations your new product time-to-market can accelerate. Companies like NEO Tech are partnering with OEMS to provide nearshoring experience and solutions that result in increased flexibility and cost savings.
China manufacturing still offers attractive and compelling solutions for high velocity supply chains as there is significant capacity and economy of scale of the manufacturing infrastructure to support these products. Also the China and Asian markets themselves are rapidly growing and there are many products where the landed cost in Asia gives preference to locally produced goods. So China is still an attractive location but the strategy and product mix built in China continues to evolve.
To find out more about NEO Tech’s nearshore solutions, contact the company at 9340 Owensmouth Ave., Chatsworth, CA 91311; 818-495-8617; E-mail: ; Web site: www.neotech.com.
Skyscraper 1
Skyscraper 2
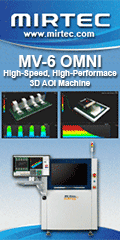
Skyscraper 3
