Altus Group
The use of AOI machines is a popular method of inspection, especially in today’s increasing use of microelectronics. AOI is the automated visual inspection of PCB manufacture which uses a camera to scan the assembly for defects that would lead to board failure. It can be used at many stages through the manufacturing process including bare board inspection, solder paste inspection and populated board inspection (pre and/or post reflow).
2D AOI was introduced in the early 80s and continues to be one of the most popular forms of inspection today, however with the ‘micro’ trend on the increase and the use of multiple stacked dies in components, due to the small footprints being used, is the 2D AOI inspection method working?
While many customers felt that 2D AOI was ‘good enough’ for their commercial application, with the increasing interest in 3D AOI technology, they also felt the need to benchmark the technology and were happy to participate in demonstrations of full evaluations.
Metrology-based inspection provides repeatable results, false calls which frequently led to escapes are mitigated substantially by basing the inspection process on measurement. Programming time and tuning times are also reduced significantly, the process of program creation is based on accurate measurements rather than subjective calls by the programmer on variable images.
The 3D AOI improves the measurement accuracy by providing true measurement of features and detecting aspects like ‘lifted leads’ or slight changes in ‘co-planarity’. This enables the detection of process drift and allows correction of potential problems before they end up as expensive value added boards having to be scrapped.
Measurement accuracy is increasingly important within the electronic assembly industry with the decreasing geometry of components used in modern electronic assembles and the need to offer 100% reliable and traceable processes for critical applications. This is especially apparent in the automotive, aerospace and telecoms industries, but is becoming increasingly important to most manufacturers as they strive to improve reliability of electronic assemblies.
The development of 3D AOI inspection has led to a step change in product quality. Greater visibility of problem areas with the ability to measure features monitor process changes and take corrective action before the line starts producing failures. Without this, process changes, such as screen print deposition go unnoticed, boards are assembled and may pass 2D inspection, but with insufficient solder paste in some areas the joints may be prone to early life failure. In the worst case, they may pass functional test and be used in an assembly which ends up in a critical part. For example, the world’s leading car manufacturers do not want ABS modules causing brake failures in the field, where recalls and litigation cost could run to millions, so will insist on the sub-contractors making such parts from tried and tested AOI systems which they have qualified after exhaustive testing.
Altus Group has seen first-hand how the trend towards 3D AOI has grown; “The use of smaller and smaller packages within components has forced the industry into looking at new methods of inspection. 2D AOI simply cannot sufficiently inspect assemblies well enough. This has paved the way for 3D AOI technology,” said Richard Booth, Altus’ managing director.
“For the past 10 years we have worked closely with Koh Young one of the world’s leading full 3D Solder Paste Inspection (SPI) manufacturers. As the exclusive representatives in the UK and Ireland of the company’s products we have seen a huge change in the number of enquiries for 3D AOI systems like the newest offering ‘Zenith’.”
Zenith full 3D AOI System measures the true profilometric shape of components, solder joints, patterns and even foreign material on assembled PCBs with patented 3-dimensional measurement, overcoming the shortcomings and vulnerabilities of traditional 2D AOI. As the first true 3D AOI system ever developed, Zenith uses 2D and 3D information for better visualisation of the components and solder joints allowing a true comparison with the IPC-A-610 standard for inspection.
Koh Young and Altus first worked together in the SPI field when 3D measurement of solder paste deposits were very much a new technology. The systems were developed to a very high degree of sophistication allowing measurement of size, shape and volume of deposits, spotting trends before they reached a point where the solder deposit was outside the manufacturing process window and led to failures, after reflow.
Closed loop process control with the screen printers all but eliminating process related problems emanating from the critical screen printing process. This is of considerable importance with the ever-decreasing size of components.
This wealth of experience led to the development of unique 3D AOI systems which utilised the same technology and allowed a level of inspection and measurement from the AOI systems which simply was not possible from the traditional 2D AOI which are still in use in many areas.
Today, Evaluation results consistently prove that Koh Young is one of the best solutions on the market, outperforming other suppliers including international OEM and CEM electronic manufacturing companies.
Koh Young is, and has been for the last three years, a 40% global market share leader in SPI, with its nearest rival at less than 20%, and securing a bigger and bigger market share in AOI.
“This trend towards 3D AOI is on the increase in all industries. We have seen figures to suggest that the AOI system market was valued at USD 346.4 million in 2015 and is expected to reach USD 1,008.8 million by 2022, growing at a CAGR of 17.1% between 2016 and 2022 (marketsandmarket.com).
“This research backs up our forecast for a steep increase in the technology. We are pleased that we are at the forefront of this surge with our relationship with Koh Young, as well as other quality suppliers of the technology.”
Skyscraper 1
Skyscraper 2
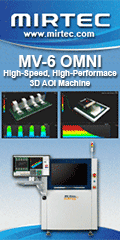
Skyscraper 3
