With the help of a strong industry partnership, the company not only survived a potentially devastating flood but came out of it stronger than before.
By Rob Cardenas, Production Manager

Ember Industries is a full-service EMS provider in San Marcos, TX. The company has grown from a small design firm to what it is today because of its commitment to quality and to taking care of its customers.
Headquartered in Texas, Ember Industries is a full-service electronics manufacturing services (EMS) company that provides full turnkey assembly of printed circuit assemblies, electronic and electromechanical devices, wire, and cable and wire harness assemblies. Ember Industries serves a diverse group of customers throughout the commercial and industrial markets. Its customers’ products serve the healthcare industry, access and security markets, high-intensity LED lighting sectors, professional audio equipment, and various test and measurement equipment that cross several market segments.
The company was established in 1986 as a small contract design firm. Through the years, it has progressed into a full-service contract manufacturing company. CEO Tom Leonardis said that Ember’s first focus has always been to provide the best service and support as possible to its customers. This focus has helped the company grow into the successful organization that it is today.
Leonardis added, “We are committed to continuous improvement and use state-of-the-art systems and best practices to benefit all customers and stakeholders. We achieve customer success by providing our customers with quality, reliability and service that exceed expectations.” As such, Ember’s capabilities are advanced and relevant to today’s most challenging technologies. These include automated SMT and through-hole technologies, ball grid array (BGA) placement, automatic optical inspection (AOI), in-circuit testing (ICT), automated and function testing, cable and wire harness assembly and testing, manufacturing process management (MPM), and integrated process control and documentation.
Ember Industries provides a complete portfolio of EMS services using documented and streamlined processes to handle all its customers’ needs from prototyping to medium-volume manufacturing and assembly. It begins with fully engineering the project by using a PCB assembly solution for machine programming and document generation in an easy-to-understand graphic representation. The extensive documentation procedures provide a reliable, repeatable process that ensures the same high-quality product each time the project is run. This engineering and production documentation, coupled with Ember’s various levels of quality metrics, creates an extensive history of every product produced, and is the basis for its continuous improvement initiatives.
Ember Industries has implemented a full ERP system that allows instant access to the production process including WIP tracking, material control, labor analysis and complete historical database such as lot numbers, date codes and serialized numbering of lots and complete ECN history.
In addition to the strong services and capabilities it offers, Ember Industries is an environmentally conscientious company. It is fully compliant to the requirements of the RoHS initiatives and recycles much of the waste materials and byproducts resulting from the assembly process.
“We are committed to the continuous improvement of our quality, costs and efficiencies as evidenced by the various awards presented to us from our customers, suppliers and associate organizations,” added Leonardis. “We recognize that we are a small part of the communities where we work. We believe in giving back to the community and the people who have supported us through the years.” Ember’s employees have volunteered and served on public boards, community organizations, and public service organizations. Company employees have organized and participated in many service organization events to raise funds for organizations and individuals in need of assistance from others.
Ember believes that strong employees make for a successful company. As such, it has worked hard to put together a strong production staff. Each member has extensive experience in the electronics assembly industry. The average years of experience of the company’s production staff exceeds 10 years, its engineering and manufacturing management team has more than 25 years of experience in the manufacturing of electronic assemblies, and its senior management team has an impressive history in growing and managing successful organizations while improving profitability and increasing stakeholder value.

Rob Leonardis, President of Ember Industries, and his production team believe that Juki Automation Systems provides the best quality to cost ratio available.
Leonardis also said that the company’s success has been realized through a business model that achieves its core competencies while partnering with technology leaders to provide all the necessary components of a complete solution for its customers.
One such partner, Juki Automation Systems Inc., has been working with Ember Industries for almost 10 years. “When it was time to upgrade our SMT equipment, we looked at the marketplace and compared competing systems. We did have some experience with a small semiautomatic machine that was made by Juki and marketed under another name,” he added. “Our engineers felt that the Juki equipment was bulletproof. Additionally, they said that the equipment was easy to set up and operate, and urged us to consider Juki in our buying decision. That started what we consider an outstanding relationship.” Ember began acquiring Juki 2050 and 2060 series pick-and-place machines in 2006 for additional capacity. In 2007, it purchased another machine to replace an older piece of equipment. Then the company purchased and installed another line in 2011, and expanded that line in 2014.
Ember currently operates six Juki pick-and-place machines on three lines. Additionally, it has purchased screen printers and reflow ovens from Juki, as well as uses various software tools provided by Juki to improve operational efficiencies. Leonardis added that in the contract manufacturing environment, the Juki systems have provided the company with a significant amount of range in part types that the systems can place. This, in turn, has allowed Ember Industries to have a large portfolio of customers from different industries.
Besides offering flexible, reliable equipment, Juki Automation Systems believes a strong partnership must include strong customer support. Leonardis confirms that Juki’s service and support is outstanding, and that Ember Industries receives a multifaceted customer service approach:
• Sales customer service is prompt and face to face, delivering product in a timely manner, and providing useful information and/or recommendations.
• Engineer customer service provides knowledgeable step-by-step assistance over the phone on any issue concerning machine software or minor hardware problems.
• Field customer service reps are second to none when it comes to hands-on troubleshooting. They deliver assistance in a timely manner and are very knowledgeable in every area of the machines.
Ember saw Juki’s belief in customer support firsthand when it experienced a devastating flood over Memorial Day weekend 2015. Juki was instrumental in getting new equipment installed as quickly as possible.
The flood occurred in the early hours of May 24, 2015. Leonardis said that the company sustained considerable damage as the flood water level reached 33″ throughout the building. The Juki systems in operation at that time were completely ruined. As a result of the flood, Ember was in cleanup mode for the next several weeks. Juki delivered and installed new SMT lines that were in operation around June 22. As cleanup continued, the company was able to bring additional operational functions online.

After Ember Industries experienced a major flood, Juki’s Chris Guest worked closely with Leonardis and the rest of the Ember team to get the company back up and running with as little downtime as possible. Ember did not lose any customers as a result of the catastrophe that sent 33″ of water coursing through its San Marcos facility.
“Chris Guest, our sales rep, was onsite on Monday, May 25. Within a couple of days, Juki had made a commitment to Ember that it would get us back up and running. The first of the three new lines was installed and operational around June 22. We had visits from stakeholders, suppliers and customers who were in awe at how quickly we were up and running,” continued Leonardis. “There is no doubt that without Juki’s involvement in our recovery, we would not have been back in operation as quickly as we were. Chris was here and orchestrated the ordering, delivery, installation and setup of the new Juki lines.”
Chris Guest said very matter of factly, “These are not just my customers, they are my friends and business associates. Their families count on me in the same manner as I count on customer loyalty. For many of these customers, Juki is their “disaster recovery plan.” In Rob’s case, they needed 27 systems to replace the three lines lost to the flood. By that Monday afternoon, we had 24 of these systems identified and ready to ship as soon as the facility could be ready. We had three loaners ship as well to make sure the recovery was complete as their preferred systems were shipped from the factory. As soon as Ember got the clearance to place equipment, Juki’s team was onsite and had the first line producing boards within a couple of days. This is what we do. Customer service and support is defined by needs, not Webster’s dictionary or as a tagline that disappears when the deal is closed.”
Ember Industries did not lose a single customer as a result of the flood and subsequent downtime. The company kept its customers informed of its progress while rebuilding the operations. Leonardis added that customers were extremely patient and understanding of the situation and even offered assistance during the recovery.
“I firmly believe we are a stronger company than before the flood. We know that we can survive a major crisis. Our relationship with our customers has strengthened. Our relationship with our suppliers has strengthened. Our employees worked diligently in very harsh conditions during the cleanup stages. We are all grateful that no one was injured. Some of our folks lost their homes or belongings and our fellow employees came to their aid. Yes, we are stronger today,” concluded Leonardis.
For more information about Ember Industries, Inc., contact CEO Tom Leonardis or Rob Leonardis, President, at 321 Carlson Circle, San Marcos, Texas 78666; 512-396-1911; E-mail: ; Web site: www.emberindustries.com.
To learn more about Juki Automation Systems and its comprehensive range of industry solutions, contact Chris Guest, Regional Sales Manager, at 507 Airport Blvd., Morrisville, NC 27560; 512-831-1880; E-mail: ; Web site: www.jukiamericas.com.
Skyscraper 1
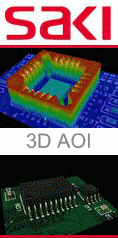