Yamaha Motor Corporation, USA announces new developments in software features and functions for its Modular Mounters (SMT placement systems) that improve productivity and simplify maintenance. These include improvements in Nozzle Health Care, Maintenance Monitor, e-Vision, and a New Grouping optimization.
Nozzle Health Care checks nozzle health after cleaning or periodically as determined by the user. The machine examines the outside of the nozzle for the presence of dirt or foreign objects, and checks functionality, including clogging, center correction, and O-ring health. The system will automatically self-diagnose nozzle appearance and functionality, and replace any faulty or flagged nozzles with spare ones without interrupting production.
The new Maintenance Monitor simplifies maintenance by helping the operator implement a maintenance plan, all guided by a simple-to-follow Maintenance Monitor interface. The Maintenance Monitor stays on top of a number of functions and alerts the operator when periodic maintenance is required. It also can show when future maintenance tasks are due, as well as a chronological log of previous maintenance actions completed. The Monitor helps the operator plan a detailed, customized maintenance routine for the machine in its unique production environment.
e-Vision helps the operator fine-tune machine performance, enabling operators of moderate skill levels (rather than higher-level engineers) to perform optimization functions including automatic algorithm selection, automated part size measurement, and auto part tuning. These optimizations allow the machine to measure part parameters automatically, rather than manual measurement by the operator, speeding up setup, improving placement performance, and minimizing part dumping.
The New Grouping Optimization feature is a production planner that is especially helpful for High Mix /Low volume production environments typically found in Contract/EMS assembly facilities today. The manufacturing engineer can use this tool to optimize planned production for a shift, providing such information as estimations for run times and changeover, along with the most efficient setup to minimize setup of feeders and exchange carts. The software will make decisions for multiple products in one setup to maximize the productivity of the line by minimizing changeover requirements. Based on commonality of components, reflow profile, and combining top and bottom requirements, engineers then set their own priority and classification to define the individual groups. The benefit is a reduction of feeders setup and changeover time resulting is a higher utilization of machine efficiency.
For more information, visit www.yamaha-motor-im.com.
Skyscraper 1
Skyscraper 2
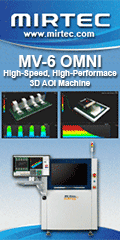
Skyscraper 3
