By Freddie Chan, KIC
In my job, I spend a significant amount of time visiting customers to gain insight into the challenges they face, what they are trying to achieve, what makes them successful and more. I need this insight to help them improve, and to provide input to our R&D team for future product development. One interesting insight I have gained can be illustrated by the following exchange:
Q: What is job #1 for your reflow oven?
A: It is to melt solder.
Q: What else?
A: Solder the assembly
Q: What else?
A: Make strong solder joints.
Q: How?
A: How? Are you asking how the reflow oven melts solder, solders the assembly & makes stronger solder joints?
Q: Are there restrictions to how the reflow oven achieves the strong solder joints?
A: Yes, you cannot damage the components, nor the board itself.
So, the reflow oven is supposed to create strong solder joints within certain limitations. Those limitations are measured by what is called a thermal profile which is compared to the process specifications set by the component, solder paste and substrate providers. It needs to create an in-spec PCB profile. In other words, the reflow oven is a “profile making machine.” The reflow oven has other obvious responsibilities, such as providing adequate throughput, managing flux to avoid performance-changing build up etc. However, the PCB profile is key. Therefore, it is ironic that while a reflow oven can provide thousands of datapoints a minute on a vast array of variables such as zone temperatures, conveyor speed, O2 level, static pressure, etc., the one variable the reflow oven cannot provide is arguably the single most important: What is the PCB profile, and how does it compare to the established process window?
It is fair to say that the industry has accepted that the PCB profile must be measured. Where opinions and execution differ is what profile to measure and how often. Some factories will measure the PCB profile once a month per reflow oven, others once a shift. Some factories will not measure the PCB profile but profile a fixture. The logic is that if the reflow oven produces good quality at a certain condition, then it is a simple routine to measure the PCB profile on a fixture at that time, and if periodic profile runs on the same fixture at the same oven settings result in a similar profile, then the oven has not changed and, therefore, the reflow oven will continue to provide the same quality on all PCB assemblies with the same conditions.
Verifying the PCB profile on a fixture rather than the PCB assembly leads to a discussion on machine monitoring vs. process monitoring. I do not think that these two concepts are at war with each other, nor are they mutually exclusive. Machine monitoring is important for a range of reasons such as information for the preventive maintenance technicians, and for troubleshooting purposes. If the fundamental question from the client is “Were my assemblies processed in spec?” only process monitoring will reveal that. It also is commonly accepted that the PCB profile can change without machine changes, or at least without timely changes in the machine. Two examples illustrate this: The tendency for exhaust and thermal load changes to impact the PCB profile without any (or any timely) response from the reflow oven.
The other dimension to this debate is the frequency of profile runs. Whether running a PCB profile once a month or once a shift, the thermal process is being run blind. The client that wants to know whether his assemblies were processed in spec may be satisfied to know that the minute before production began, the reflow oven produced an in-spec profile. More clients want traceability and evidence that the profile for each PCB assembly was correct. That condition requires a continuous and automatic thermal profiling system.
It makes sense that if the fundamental responsibility of a reflow oven is to profile an assembly within the process specifications, then that profile must be measured and monitored. The SPI monitors the output from the printer in terms of X, Y and theta accuracy, the component placement machines will monitor its output, or an AOI machine will do so, why not the black box reflow oven?
For more information, contact President Bjorn Dahle at KIC, 16120 Bernardo Center Dr., San Diego, CA 92127; 858-673-6050; E-mail: ; Web site: www.kicthermal.com.
Views
Skyscraper 1
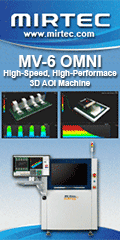