By Freddie Chan, KIC
Two of today’s most important areas of focus in the electronics manufacturing industry are equipment utilization and defect elimination. Equipment utilization because, in many assembly operations, this is the single biggest contributor to cost or profit improvements. Eliminating defects is important because poor quality is expensive and a growing segment of the market no longer accepts rework.
I have had an untold number of discussions with process engineers that essentially go like this:
Q: Percentage-wise of all defects in your SMT line, how much does the reflow process contribute?
A: Oh, it is hard to measure because it can be difficult to determine the root cause of a defect. For example, cold solder on a bottom connected component (BTC) can be due to either a printing or reflow problem.
Q: Can you venture a guess?
A: Reflow soldering is responsible for only a small portion of the defects, likely less than 10%, and probably less than 5%.
Q: Okay, let’s say that you are running your PCB assembly hour after hour & day after day without a problem and then suddenly you catch multiple defects in your inspection process, be they AOI, X-ray, ICT or other. You decide to shut the line down to identify the root cause. What do you do?
A: If the cause of the PCB assembly defect reveals itself immediately in the inspection process that caught the problem, then we go to the source and fix it. Often, however, the root cause is not immediately clear.
Q: What do you do then?
A: We run a thermal profile.
Q: You just told me that 95%+ of the time reflow soldering is not the problem. Why do you start there?
A: Well, we have pretty good information from all the machines and processes due to SPI and AOI except the reflow oven where we rely on weekly or daily spot checks (running a manual thermal profile). Additionally, we can see directly into most of the machines. Again, the reflow oven is the exception because it is sort of the black box of the production line. So we run a thermal profile.
Q: Does that mean that 95% of the time you are looking for a problem where it does not exist?
A: Well, not exactly 95% of the time because sometimes the root cause of the yield issue is apparent and does not enter into this equation.
Q: How long does it take you to run a thermal profile when you have an acute issue like this where you have shut down the PCB assembly line due to a sudden yield issue?
A: It varies, but it may take longer than a normal scheduled thermal profile run because we need to retrieve the thermal profiler and the relevant printed circuit board with TCs attached. Hopefully, we can run the profile within 15 minutes but sometimes it can take more than 30 minutes.
Most companies calculate what every hour of unscheduled downtime costs them. The actual numbers vary from factory to factory but the calculations that I have seen indicate that reducing downtime by one hour per week per printed circuit board assembly line results in a profit increase of approximately €50,000 per line per year.
Moving from a reflow oven spot check to continuous process monitoring, or automatic thermal profiling system, provides the responsible engineer with instant information whether the thermal process is the culprit or not. No time is wasted looking for a problem where it does not exist when very expensive downtime seconds are ticking away. Additionally, should the thermal process be the root cause, then the monitoring system will provide information to help pinpoint where in the oven or process the adjustment needs to be made, hence enabling the engineer to identify the problem and fix it quickly to further reduce unnecessary downtime.
This example also illustrates the benefit of smart machines in the context of Industry 4.0 or the Smart Factory, namely how real-time data in an actionable form enables engineers to run production lines and the factory more effectively. The scenario described here represents one of the “low-hanging fruits” that instantly leads to significant yield improvements. From this basic capability we can quickly identify other opportunities to improve equipment utilization and yield. When visualizing the real-time thermal process data on SPS charts on a dashboard, negative trends such as a falling Cpk number become apparent. Since changes in a reflow oven tend to be slower, an SPC chart can provide early information about what might happen in the future. Therefore, in some cases, it is possible to entirely avoid unscheduled downtime by alerting the maintenance personnel about the trend. Then, they can address the issue during the next preventive maintenance event when the line is shut down anyway. This philosophy of preempting the problem becomes more and more important as factories strive for perfection and yield improvement where rework is unacceptable and a defect equals scrap.
So how big is this issue? At some IPC APEX EXPO 2017 roundtable discussions, a statement was made that an average factory in North America runs production only 67% of the time. In other words, 37% of the time the production line does nothing except erode profits. Clearly this surprisingly low equipment utilization is caused by many factors beyond yield stoppage, especially the growing number of line changeovers. But as the calculations above indicate, we need to explore opportunities to reduce this number because every downtime minute is expensive. There appears to be ample opportunities to capture some of the low-hanging fruit for a return on the investment measured in weeks rather than years.
For more information, contact President Bjorn Dahle at KIC, 16120 Bernardo Center Dr., San Diego, CA 92127; 858-673-6050; E-mail: ; Web site: www.kicthermal.com.
Views
Skyscraper 1
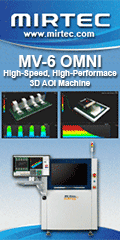