By Vitor Barros, KIC Europe
Industry 4.0 is one of the most exciting developments in the manufacturing industry in decades. It promises vast improvements for both manufacturers and their customers. For some companies, however, it can be overwhelming, and it can be difficult with the current available information to understand exactly what the benefits will be in the average factory, and to calculate the return on the investment.
Therefore, it may be helpful to bring the discussion down to a tangible level and to isolate one little part of the whole smart electronic assembly factory, namely reflow.
For many years, reflow oven manufacturers have done a great job improving ovens. The ovens keep getting ever more stable and more efficient. Next step is to acquire, analyze and share data in order to run the ovens and the entire factory more effectively. If you ask a process engineer what the ultimate job of a reflow oven is eventually you will learn that a reflow oven needs to solder the assembly in accordance with the solder paste, components, and substrate tolerances or specifications. This is also called the process window, and is measured with a time temperature profile. So we can think of an oven as a “profile-making-machine.”
Now, the engineers and their customers want to know whether the PCBs are produced in-spec. So they take great care in selecting a combination of temperatures and conveyor speeds to create the correct profile on the PCB, along with settings for nitrogen, vacuum, air flow or other variables when required. They also do spot checks by running a manual profiler through the oven from time to time. That is how most electronic manufacturers operate today.
In comes the smart oven. What is it? What are the real tangible benefits to the user?
Volumes have been written about Industry 4.0 or smart oven technologies, but since this piece aims to discuss the concepts in very down-to-earth concrete terms, let us first focus on what the technology will do for the electronic manufacturer. After all, smart technologies need to serve a purpose, and the benefits need to far exceed the investment. When boiling it all down to the core, we are left with two components:
1. Eliminate the waste
Downtime: According to an IPC study, the average electronic factory has 37 percent downtime
Scrap or rework
Time: According to a recent study, the average engineer spends 40 percent of his time looking for people, equipment, information and more
Unnecessary energy consumption
Manual tasks
Anything short of perfection
2. Provide required documentation such as traceability and genealogy
The beauty of much of these new capabilities is that they can be measured and we can run ROI analysis on the smart oven investments. Each factory will have a unique set of cost factors but the calculator below shows ballpark figures to illustrate how this works. Figure 1 calculates the impact on this particular factory when reducing unnecessary downtime by two hours per week. The annual profit increase is €67,000 per production line. If we assume an initial investment of €20,000 to upgrade to a smart oven, our ROI is 3.5 months.
Figure 2 includes an increase in first pass yield from 96.0 to 96.5 percent. The resulting annual profit increase is €81,000 per production line with an ROI of 2.9 months.
The numbers look interesting since they represent profit increase per line per year, and we have only calculated a couple of the many benefits that smart oven technologies represent. Now, what is this stuff and how does it work? The actual technology execution may vary from vendor to vendor, but Industry 4.0 technology will include the following components:
Full automation
Process transparency and traceability
Flexible production capabilities (fluid production changeover and ramp up)
Connectivity
Energy efficiency
Data analytics
Machine learning
Retrofitability
There is little space to describe the technology in details here, so here is the executive summary.
Process optimization / oven setup / fluid changeover / automation
A reflow oven has billions of alternative recipes. Smart optimization software will do an exhaustive search of all of them (in a few seconds) and select the optimum based on user criteria. For example, to reduce oven changeover time (oven frequently is the slowest machine in the production line to change over) the software identifies a common recipe for a wide range of products, or it will search on different conveyor speeds while keeping the zone temperature settings fixed.
Process transparency / trace ability / automation
Embedded sensors in the oven calculate each PCB’s profile on the fly and compare it to the established process window. The system can instantly alert on out-of-spec situations or warn about an unstable process. Picture having a video camera in your oven that is always on. The profile and machine data are stored. There is full process traceability to each individual PCB. Automatic loading and verification of program is based on bar codes. Instant troubleshooting of yield issues on the line is provided.
Connectivity
Real-time data flows to the factory network and MES system. A centralized data base allows virtually instant identification of relevant date and sharing, and is accessible from anywhere on any authorized PC or mobile device.
Machine learning
Intelligent databases learn the thermal dynamic relationships with each profile and quickly provide oven setup suggestions without even running a profile. Start thinking about throwing away your profiler. Oh, did I just say that? I did not mean it.
Retrofitability
Almost all reflow ovens installed in any factory today can be retrofitted to become a smart oven.
Conclusion
Industry 4.0 technologies have matured in some areas to the point where they are affordable, and they provide real value to factories of all sizes. Embarking on this new world may seem overwhelming and fraught with risk. When focusing on a narrow scope, such as smart oven technologies that includes virtually all the major building blocks of Industry 4.0, an electronic manufacturer can move up the learning curve with low risk and low investment. Significant benefits such as fast ROI and happy customers flow quickly. Perhaps the most important benefit, however, comes from the implementation process itself. Each factory will encounter hurdles and learn what works and what does not work. For example, how OT and IT work together for a safe solution. After a few weeks to implement smart oven technologies, the company is far up on the learning curve and well-positioned to take on the much bigger Industry 4.0 scope.
For more information, contact President Bjorn Dahle at KIC, 16120 Bernardo Center Dr., San Diego, CA 92127; 858-673-6050; E-mail: ; Web site: www.kicthermal.com.
Views
Skyscraper 1
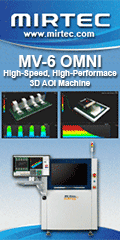