(Or are we “Reelin’ in the Years”)
James Cawkell – Adaptsys
Tape and reel packing of surface mount electronic components is now well established and widely used by circuit board assemblers and electronic device manufacturers the world over. The technique is now also becoming rapidly taken-up by mechanical assemblers and manufacturers of electro-mechanical devices to help automate their production lines. But have you ever stopped to remember what life used to be like in the days before this simple idea hit the factory floor?
It’s actually a really important question as we look towards the EU referendum, because the best way to summarise the answer is; “We moved production to Asia to save money.”
Back in the 1980’s not long after the last EU referendum, electronic products were complicated and labour intensive to make, and therefore expensive. The price of labour throughout Europe was rising rapidly, and in the search for cost savings someone realised that Asia had a massive and un-tapped reserve of cheap labour. Japanese companies were making huge strides to simplify the design of electronic products (making them more reliable and just ‘better’), but European brands simply had to do something to keep pace.
The answer then was to follow the service industry example (which had already started moving software development and customer service to India) and ‘make in Asia’. Taiwan and Hong Kong were the first destination for many manufacturers, who manufactured there and shipped finished products back to Europe. Once China started to open its doors to international trade during the 1990s, ‘offshoring’ as it became known was all the rage.
Now however, 30 or so years later, things are swinging back. China is now the second biggest economy in the world with a huge demand of its own for products, and labour prices across Asia (though still lower than Europe) are rising rapidly. The financial savings of labour on the other side of the world are rapidly eroding. Added to that, the placing of more and more function onto integrated chips has increased product capability and reduced (relatively) the number of components on each board. So how to make savings now?
The answer now is increased automation, which has actually been quietly going on in parallel to off-shoring since the mid-80s.
Automation of surface mounted component assemblies levels the playing field. Essentially, everyone can use the same automation technologies where-ever they are in the world. But that also means they pay roughly the same price to use those technologies, which in turn means that as labour is now a smaller part of the overall assembly cost, so it plays a smaller part in the equation of where and how to make things.
Another trend that has grown more recently is mass customisation, and again, this has a big influence on where manufacturers make their products. Essentially, mass customisation is all about making products more responsive to the market. That can take many forms; from creating an ‘own label’ version for a big retailer to making ‘limited editions’ to celebrate a significant event, or else short-runs of highly specialised but high-value or mission critical equipment. These can of course be made anywhere, but making them nearer means a more effective design and specification process, simplified import procedures, shorter lead times and significantly reduced transport costs.
Even here, tape and reel creates another twist in the geo-economics of electronic products. Manufacturers are now using the technique to package small sub-assemblies that are common to many finished products, particularly where fitting mechanical components has to involve some level of manual assembly. These can then be packed in tapes and shipped to Europe for automated assembly in short-run and customised products, taking advantage of both relatively cheap labour and automation in the same process.
Tape and reel component packaging, first patented in the mid-80s, has been a key part of the infrastructure needed to make all this possible. By ensuring the safe, predictable delivery of components to the automated point of assembly tapes have increased product quality and production-line through-put. And they have changed the cost model upon which Europe is taking back control of its own manufacturing and allowing businesses in Germany, the UK and in all the other 26 nations of the EU to once again make high-quality, innovative electronic products in our own continent.
As labour costs and transport prices around the world continue to climb, tape and reel packing systems are playing their part towards recreating the manufacturing optimism that existed throughout Europe after the last EU referendum. Does that mean they will influence the outcome of this referendum? Probably not. But in or out of the EU, Britain’s electronics industry (and that of Germany or any other EU country) would not be able to compete on the world stage without ‘tape and reel’.
For further information visit www.adaptsys.com
Skyscraper 1
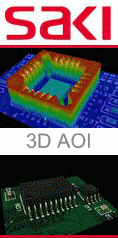