Author: Phil Kinner, Head of Conformal Coatings Division, Electrolube
Introduction
In a typical car today, electronic systems are critical to the smooth and safe operation of the vehicle. Even before the engine starts, electronics have already unlocked the car. Once you start the engine and step on the accelerator, sensors assist in getting out of your parking space, engine control units (ECUs) tune the engine performance, monitor the pressure of the tyres and safety systems are powered up in standby mode. As you pull away, adjust the air conditioning, ensure your phone is connected to the entertainment system, set your destination on the satellite navigation system and initiate your favourite music, yet more electronic systems are brought to life.
The electronics continue to manage your interior temperature through the Heating, Ventilation & Air conditioning (HVAC) system. Sensors and control systems detect crash situations, deploy airbags and side impact protection and can automatically notify the emergency authorities of the location of an accident should the driver be incapacitated. Braking is controlled to prevent dangerous situations such as locked brakes, automatic transmission and management systems are used to change gears, maximise fuel efficiency, monitor and minimise emissions. Active collision detection systems use cameras and radar systems to alert drivers of impending situations and prevent lane drift.
The usage of automotive electronics will continue to develop as consumers demand ever more performance, safety, comfort, convenience and entertainment from their vehicles. Systems are being developed that will do even more to avoid accidents, protect and entertain occupants and reduce the environmental impact of the journey.
The value of the electronic systems in today’s vehicle routinely exceeds 20% of the total vehicle value and many estimates take this value to greater than 35% during the next 5 years. With the increased adoption of electronic vehicles, and the development of the Internet of Things, which has culminated in the futuristic driverless car being tested by Google in California and BMW on the roads of Bavaria, the future could not look any more different to the industry in the 1970s when electronic fuel injection systems were first introduced to mainstream production.
Much of the increased automotive electronics usage has been enabled by the development of even more powerful controllers, sensors and switches, as well as the development of low-cost, high reliability electronic systems which have made body, comfort and safety applications standard in most modern automobiles.
Low-cost, high reliability
With increased demands for sophistication, performance and reliability, 5 and even 7 year warranties are being supplied with new vehicles and the need to ensure reliability at acceptable cost of new designs is one of the greatest challenges facing the component suppliers. Electronic systems are increasingly facing wider temperature extremes, greater degrees of humidity, condensation and yet more corrosive gases. With the drive towards electric vehicles, with much higher voltages being normal, increased dielectric protection is required to enable designs to be sufficiently dense to meet size and weight constraints. The increased sophistication of the electronic systems often means they are more sensitive to contamination and the impacts of the external environment. With the increased level or interconnection between systems, failure in one assembly can have a knock on effect into another. Unlike aerospace applications where there may be 2 or 3 layers of redundancy in design, automotive designs typically must work, first time, every time throughout the life of the product.
Conformal Coating to increase reliability.
Conformal Coatings are thin, protective polymeric coatings that are often used to provide the required environmental protection, without an excessive cost or weight increase. Conformal Coating applications are generally thought of being either ‘in-cabin’ electronics (situated within the passenger cabin) or ‘underhood’ (near the engine) electronics. The two distinct categories make it convenient to discuss the main requirements of each, but of course, with increased sophistication and multiple functionality of assemblies, the traditional environments continue to merge, and the drive to higher power electronics in electric cars blurs the lines further.
‘In-cabin’ automotive electronics
Electronic sensors and systems situated in the passenger cabin, essentially occupy the same space as the vehicle occupants and are therefore exposed to largely similar environments. In the winter, that can mean extreme cold and the tendency towards a condensing atmosphere. In the summer, the tendency is towards a warm and humid atmosphere. Condensation and high humidity are both a risk to the reliability of electronics, by promoting the formation of corrosion. In addition to these factors, the electronics may be exposed to atmospheric pollutants, cleaning solutions, liquid splashes etc. Any of these factors may be a potential reliability risk, especially in association with humidity and condensation.
Corrosion is a complicated electro-chemical process, with a variety of potential mechanisms and causes, well beyond the scope of this article, however, in the vast majority of cases, there are 3 requirements that must be fulfilled in order for corrosion to take place.
Intrinsically electrochemically dissimilar metals (e.g. Gold/Silver and Nickel/Tin), or the creation of an anode and cathode by application of applied bias.
The presence of an ionic species (usually Salts, Halides, Hydroxides etc).
The presence of mono-layers of condensed water, to dissolve the ionic species resulting in an electrolyte solution.
In order to prevent the possibility of corrosion, it is necessary to remove one of the pre-requisite conditions.
The choice of metals is limited to those used in the solder and solder finish chemistries, which are dissimilar, and there will always be areas of potential difference due to the nature of an electronic assembly. Cleaning can help remove ionic species, but cannot prevent the re-deposition of ionic species from the operating environment.
Conformal Coatings help prevent the formation of electrolytic solutions by acting as moisture barriers. The coating needs to be a good barrier against moisture and must have good adhesion to the substrate to prevent delamination. Once the coating is delaminated, moisture can eventually collect in this ‘pocket’ and form an electrolytic solution with any pre-existing ionic contamination. This is the reason that cleaning prior to conformal coating is recommended, to provide a powerful synergistic elimination of two of the three pre-requisite conditions for corrosion.
Given the relatively benign operating environments experienced by ‘in cabin’ electronics, Acrylic conformal coatings have historically dominated this segment, offering good all round properties, especially against high humidity and spills and splashes.
‘Under-hood’ Electronics
The main differences between the requirements for the protection of ‘under-hood’ electronics and ‘in cabin’ electronics are due to the placement of the former. The environment can be much less controlled, with higher maximum operating temperatures and far more opportunity for contamination by fuels, oils, cleaning fluids, corrosive gases, metal particulates and salt-water slush sprayed up after road gritting etc.
In short, ‘under-hood’ and other non-cabin electronic assemblies are required to provide protection under much tougher environmental conditions.
The next generation of protective coatings
In order to counter these challenges, a new type of protective coating is required. These coatings are required to be extremely resistant to wet conditions, chemical resistant, highly flexible to survive thermal shock excursions and temperature resistant to survive the higher operating temperatures.
To counter these challenges, Electrolube has developed a new range of highly durable, solvent-free, modified polyurethane conformal coatings, which are designed to be applied at a greater thickness than regular conformal coatings and cure within 10 minutes at 80°C, re-using existing thermal curing ovens often used in solvent-based processes.
Condensation / liquid water resistance
‘Sharp-edge coverage’, the ability to completely and reliably cover device leads, solder joints and other metal surfaces, to prevent them from being susceptible to corrosion is a long-standing, well known issue, that has recently been highlighted by the IPC5-22ARR J-STD-001/Conformal Coating Material & Application Industry Assessment.
To demonstrate the importance of edge coverage and protection from liquid water, in the form of condensation, the National Physical Laboratory (NPL), UK are currently working on the development of a controlled condensation test. They have shown that at 40°C and 93%RH, a temperature differential of just 1.5°C can lead to the formation of a sufficient moisture to reduce the surface insulation resistance of a copper coupon from TΩ to 1MΩ (limit of detection).
The data clearly shows a significant drop in the SIR value of an uncoated assembly, limited protection by both the Nano coating and the single-coated acrylic, improved protection from the double-coated acrylic, with both the new urethane materials providing improved protection, whilst UR3 in particular shows outstanding protective capabilities against condensing water.
This can be explained in part by thickness and coverage, although the particular chemistry of the formulation also plays a significant role, as explained by the significant difference in performance between UR4 and UR3, even though the applied thicknesses (c. 150µm) are similar, as shown in fig 3 below.

Fig 3. Cross-section of 3 Oz Coated Coupons, showing importance of applied thickness and coverage in condensation resistance.
Thermal Shock Resistance
Automobile electronics are usually required to work between -40°C and 125°C, with rapid transitions between the temperature extremes. The Electrolube SIR test coupon shown in fig 4 was designed, containing a number of components, laid out in a difficult configuration, to better simulate a production assembly. Coupons were selectively coated with polyurethanes UR3 and UR4 at a target thickness of 250µm and subjected to 1000 air-to-air thermal shock cycles, at the temperature extremes previously indicated, with a rate of temperature change in excess of 40°C / min.
These coupons were visually inspected at 20X magnification for evidence of cracking, delamination and solder joint or component damage. After 1000 cycles, UR3 showed some signs of surface cracking and discoloration, but did not expose any metal surfaces and did not propagate to the surface of the board, whereas UR4 showed almost no change in appearance.
Salt-Mist Resistance
In order to assess the protection provided under salt-mist conditions, intended to simulate winter driving conditions, the test coupons shown in fig 4, previously exposed to the 1000 thermal shock cycles were subjected to a 196 Hour salt-mist test (5% NaCl Solution). The coupons were continuously powered at 50V for the duration of the test and the insulation resistance was measured at periodic intervals throughout the test.
As can be seen in figure 5 below, both materials performed well, providing excellent protection against a salt-mist environment, although UR3 showed a higher overall degree of insulation resistance, in line with the results from the NPL’s condensation test.

Fig 5 – Insulation resistance of polyurethane materials under salt-mist conditions with 50V bias applied continuously.
Conclusion
In order to meet the demands of the automotive industry for greater electronics reliability under ever more adverse conditions, Electrolube has developed a range of solvent-free, higher performance protective coatings. These coatings have been developed to be applied at greater thicknesses to overcome common application defects and improve sharp-edge coverage.
These materials have been demonstrated to provide significant performance improvements on model PCB test assemblies, in terms of resistance to thermal shock, condensing and salt-mist environments than traditional conformal coatings, ultra-thin coatings or even UV curable materials.
Skyscraper 1
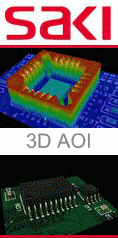