Vitor Barros, General Manager, KIC Europe
It seems like everybody is talking about the “Smart factory”/“Industry 4.0”/“IIoT”/“Made in China 2025”/“IOM” these days. But is anybody actually doing anything? The tier 1 EMS companies certainly are investing heavily in smart technologies; but, really, how relevant is this for the average electronics manufacturer?
The first question we have to ask is why? (What is the motivation for any of this? What is the justification?) Any new trend or technology is just a means to an end. So before deciding whether to invest our time and financial resources, we need to establish the goals and objectives. Likely, these will vary from company to company but, in general, the smart factory industry trend includes the following goals:
Manufacturing perfection/Make it right the first time
In the past, a broken calculator or digital camera represented an annoyance. But today electronics are everywhere in our lives, and we depend on reliable performance, not just in pacemakers and air bag controllers but in all things. Even when electronics are not mission-critical, companies still suffer deeply when their products are not reliable. Users have choices, and they have information. They can share a negative review with nearly all other potential buyers in the world instantly. Mediocre quality cannot easily hide anymore.
Eliminating human error
Reducing production cost
Enabling the flexible factory
We are entering a future of mass customization and it is already killing factory productivity. Production line utilization is bad and getting worse, and we have both fast NPI and ramp up.
Need for documentation
Process transparency and traceability down to each PCB is needed, as well as BOM genealogy.
Sustainable production
We need to reduce energy use, avoid harmful and illegal products, and participate in product lifecycle recycling.
Well that is a nice long list, but it does not necessarily help anybody decide whether to make the jump. To do that it may be helpful to divide this discussion into “have to do” vs. “want to do”.
Have to Do
A few years ago, I watched an interview with a Siemens AG executive who stated that in the second phase of their Industry 4.0 initiative (as it is called in Europe), Siemens would be working with all their vendors to comply with the new requirements. He said that because their products include parts from external vendors, all their vendors in the future would be required to develop a smart factory with the relevant documentation requirements. But here comes the interesting part: He also said that because Siemens’ vendors’ products tend to include parts from their suppliers again, Siemens would require its vendors to require their suppliers to also run Industry 4.0 operations.
So, if this philosophy takes hold, then the requirements will trickle down to smaller and smaller manufacturers.
I hear complaints all the time such as “I work twice as hard as I used to with no more pay!” Without getting into a political discussion on the human struggle in a modern society, we clearly observe that competition is being dialed up to 11 everywhere. So a factory that was successful in the past with average performance likely will not be successful in the future without significant improvements.
Want to Do
Poor quality is expensive. Low production line utilization is ruinous. Unnecessary electricity consumption is costly. The average manufacturing engineer spends 40 percent of his time looking for information. You get the drift. The smart factory can reduce production cost and improve productivity even in an environment with more NPIs, shorter production runs and frequent production line changeover.
Smart factory technologies enable real-time production and process visibility in dashboards that are accessible from authorized desktop PCs and mobile devices anywhere at any time. Engineers make better and faster decisions. Alternatively, the machines make those decisions without the need to involve a technician as exemplified by closed-loop SPI and stencil printer. The result is consistent quality, faster troubleshooting and human error reduction.
Factory engineers and managers are like circus acrobats with hundreds of balls in the air at any time. Complexity grows exponentially between different production runs, clients, job shifts, production lines, etc. Instructions are given only to leave the engineer wondering whether they were followed or not. The connected factory organizes all such tasks across the whole factory and supply chain, while verifying compliance and actual performance results.
For EMS companies, there is yet another motivation – perhaps the biggest of them all: differentiating their company from their competitors with the kind of capabilities that clients demand. These include full process control, low risk of product lifespan failure, full transparency with convenient access to traceability data, fast NPI and scale up, etc. In other words, investing in the smart factory to win more orders, and to win premium orders.
To Plunge or to Wade in?
While the benefits and ROI are positive, converting a traditional factory into a smart factory can be a high-risk project with significant capital requirements. The impact on the company and the people in it can be significant. The alternative to taking on the whole factory at once is to select a small segment of the factory and progress that to an Industry 4.0 level. When doing so, the company will encounter most of the speed bumps and challenges associated with any Industry 4.0 project regardless of scope.
One example relates to the IT-OT conflict. (Information Technology (IT) people are responsible for the efficient, safe flow of data in the factory: Avoiding viruses, losing data, hacking, back-up, etc. Therefore, IT guys are understandably conservative and protective of their domain. The Operational Technology (OT) guys want a revolution. They want machine-to-machine connectivity, extreme levels of automation, data analytics, robots, Augmented Reality, perhaps even Artificial Intelligence and more. But they need the data to run on the IT structure. So regardless of the smart factory conversion scope, a company must decide how to safely and responsibly enable data management. They must start the dialog between IT and OT, and likely will need involvement from higher level management.
Another example relates to machine-to-machine communication. Closed-loop SPI and stencil printer operation has become popular. Similar connectivities now are popping up everywhere, even between the thermal process, SPI and AOI. Communication protocols are being developed at IPC and the Hermes initiative, but they are not yet available. So any company investing in smart factory technologies must work with equipment vendors to secure connectivity and compatibility between them.
The benefit of initially focusing on a small segment of the factory is the smaller required investment in terms of capital and engineering-time. The company will quickly decipher the learning curve in a lower risk environment. Once successful, the company will be well positioned to convert the rest of the company with a faster, more effective conversion rate.
Conclusion
Smart factory conversion is no longer limited to large companies. Eventually, the average factory will be under pressure to upgrade. In the meantime, many smart factories will experience improved profit and revenue growth. This transition may seem overwhelming and risky; however, one option is to focus on a smaller scope and move up the learning curve at a lower risk and with a lower investment level.
For more information, contact President Bjorn Dahle at KIC, 16120 Bernardo Center Dr., San Diego, CA 92127; 858-673-6050; E-mail: ; Web site: www.kicthermal.com.
Views
Skyscraper 1
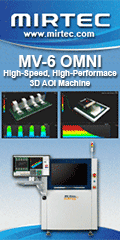