In the beginning of SMT, Vapour Phase Soldering, also well known as Condensation Soldering, was the preferred reflow soldering technology because of its excellent heat transfer capabilities. The process is widely used for assemblies with a large variable of thermal mass components on the PCB, popular in laboratories for prototype level assembly, and also with some small manufacturers. It has the advantage that it can heat large masses evenly and quickly whilst the peak temperature is controlled. It emits thermal energy by phase change of the heat transfer medium from gas-like to liquid state. This phase change, known as condensation, on the surface of the solder piece lasts until the assembly has reached the temperature of the vapour. Another advantage includes no overheating of assemblies, so vapour phase soldering is ideal for lead free solder processes.
It also offers continuous heating-up of the complete assembly, no matter what the assembly is made from; an oxygen free soldering process without the use of any protective gas and finally the efficient use of energy because of the high heat transfer, therefore reducing operating costs compared to other soldering technologies. However there were some disadvantages like fast temperature rise and nearly no influence on the temperature profiles. Due to this, Vapour Phase Soldering was reduced to special applications with high mass or complex boards in low numbers (e.g. for military or aerospace).
To combat these process challenges, SolderStar developed a new profiling system designed specifically for Vapour Phase machines. The latest evolution of Vapour Phase machines now offer much more user controlled soldering, the main advantages of a vapour phase system such as fixed peak temperature remain, but freely adjustable temperature gradients and profiles are now possible, automatically controlled time above liquidus and a perfect automatic inert gas atmosphere.
The original ‘dream’ sold by the manufactures of vapour phase soldering machines was that profiling was not needed, the reality of course in production is ‘You Can’t Manage What You Don’t Measure’. Other problems are evident in the process, usually ‘tomb-stoning’ of components. Given the even heating of the Vapour Phase process you would not expect this, but given PCB designers do not always adhere to machine manufactures recommendations they then need to be set-up by an engineer and monitored if the long term quality is to be maintained.
Whether batch or inline, atmospheric or vacuum, SolderStar developed a solution that gave users the ability to understand and control the production process and production quality. A two-piece, low mass heat-shield gives protection whilst minimising process impact, allowing operation across pre-heat, vapour and vacuum stages. Once retrieved from the process, the hot shield can be opened allowing data download and rapid air cooling, minimising the potential for instrument damage. Alternatively captured data can be transferred by wireless telemetry to any selected PC station, allowing real-time profile viewing and analysis by the user.
Soldering always means to heat up everything well enough so that soldering can be accomplished even on sockets or large BGAs, but at the same time to be sure that nothing is overheated or delaminated. So especially for lead free soldering the process window becomes very small. With Vapour Phase Soldering even FR4boards, double sided densely packed, can be soldered reliably and with no danger of overheating.
The advantages of the Vapour Phase heat transfer in combination with new machines and options offer an excellent tool for easy and defect free reflow soldering, independent whether lead free or leaded solders are used.
Machine Types and Profiling Methods
There are a number of machine types on the market. They offer different solutions in a wide range of machine sizes, starting from small laboratory equipment for prototyping, testing and rework, to medium size batch, up to inline machines for high volume production. Some of the batch machines can be upgraded to inline use later as it might be needed. Two blue-chip companies that use and recommend SolderStar vapour phase profiling equipment are Rehm Thermal Systems and IBL Technologies, both leaders in vapour phase technology,
There are several machines that benefit from SolderStar thermal profiling, one being medium size production machines. These machines are batch based and the PCBs are loaded into the basket. The basket then moves through the machine and enters the Vapour Phase chamber for preheating and soldering and exits again once complete.
This style of machine is harder to profile as some machines have internal thermocouple ports internally wired to the outside world. An external profiler can be used to capture the profile, although this is more difficult and not ideal for daily production testing.
These machines can also come with a vacuum stage. If this is employed the soldering stage uses a sealed chamber and it is not possible to get wires inside, a true pass through profiler is needed, this is where SolderStar’s system comes into its own.
Another machine process is inline, these are much more difficult to profile with long wires in the same way a long conventional reflow oven is not profiled with long wires, they snag and the results are always not always accurate. Again, if vacuum is employed you cannot use long wires.
The SolderStar PRO – VP system allows users of batch and in-line vapour phase soldering systems to fully profile their products in the same way as a conventional reflow machine. The system includes the SolderStar PRO data-logger combined with a sealed light-weight heat shield capable of operating in the pre-heat, vapour reflow and vacuum stages of the machine. Data can be passed to a nearby PC via wireless telemetry allowing the profile to be viewed in real-time by the user. Once data capture is complete the heat shield can be opened and the datalogger removed, allowing rapid cool down cycles and minimising the risk of overheating the profiling unit.
SolderStar’s product has an external data logger with long wires making them a perfect choice for manufactures with different soldering processes, wave etc. as one datalogger does it all. There is also added ‘down the wire’ logging capabilities via a USB connection, with live data which can be viewed by the engineer as the PCB passes through the machine. The pass through profiling unit is SolderStar’s main unit and is the only way to profile machines with vacuum stages, and is really is a far superior method for any Vapour Phase machine, other than laboratory machines.
The Profiler’s Enemy – High Thermal Transfer!
Because of the use of Galden vapour in the machines, the thermal transfer is very high compared to a conventional reflow oven, and subsequently the thermal protection of the datalogger is paramount to survive overheating. The vapour must also not be allowed inside the profiling unit as it will ultimately damage the electronics and insulation used. As vacuums are employed the problems increase, the system must also be able to withstand any pressure difference seen in the process, and a real-time a wireless telemetry link is required to relay data back to PC from inside the machine and vacuum chamber
There are two approaches to this problem:
The 1 box approach – a datalogger electronic PCB inside a sealed box.
Advantages – it is physically smaller.
Disadvantages – as it is perfectly sealed to withstand the vacuum, needs to be strong & hence thermal mass/weight is high.
When it exits the machine is very hot. As the unit is sealed if it is simply left it will continue to heat and damage the battery and or electronics. Force cooling is needed such as a water bath or similar.

Early solution developed by SolderStar : 1 Box style datalogger
The 2 box approach – a datalogger is used that can be separated from the protective shield when it exits the machine.
Advantages – better protection thermally and has rapid cool down. It uses SolderStar’s generic datalogger which can be used for multiple processes if required. Only one calibrated unit is needed each year, rather than multiple units.
Disadvantages – It is physically larger. Most engineers are concerned that the measurement instrument being in the process will take energy away from the vapour cloud and affect the measurement and not be a true reflection of the PCB profile. The larger it is, the more concern there is. SolderStar did not find the 1 box approach to be the favoured process.
SolderStar’s approach to the problem of ‘physically larger’ was to look laterally at the problem. The actual problem is the thermal mass of the object. They produced a ‘thin’ wall protective shield which has a large surface area, but exceptionally low thermal mass. It is Teflon coated to resist the Galden build up, and has proved to have virtually no impact on the process. The lightweight skin of the shield heats rapidly, and once up to temperature the condensing on the shield is minimal. The carefully ribbed and strengthened design, includes a pressure release system to ease opening the system after the vacuum stage.
SolderStar undertook internal testing of the system on a Asscon Quicky 450. The test was done using the smallest scale machine, which if an ‘impact’ would be seen then it would be seen on this level of machine. It allowed a profile to be captured with long wires, so no instrument in process chamber, and then with the instrument inside.
The purpose of the test was to;
1 – Further validate the thermal performance of the new VP heat shield
2 – Perform a ‘leak test’ evaluation of the new ‘O’ Ring seal
3- Monitor any effect of the thermal shield on the process
FIGURE 1
SolderStar’s Conclusion to the Internal Testing
1 – Thermal performance is adequate for most vapour phase processes, with the original spec. of 250C for 9 minutes likely to be achieved.
2 – New ‘O’ ring provides sufficient seal
3 – Both the red & green traces almost exactly overlay in the ramp up and peak stages, the green trace has a longer peak as it was left in the process longer. The ramp up slope & time are the same with the system inside & outside the barrier.
The vapour energy available within a machine like the Quicky, is less than the machines this profiling system is likely to be used within. The light weight shield is heated rapidly and energy then thermal absorption minimised, at no point did the vapour ‘collapse’ and the process be impacted.
The SolderStar system has been proven not just through in-house testing, but also through use by manufacturers. Both Rehm and IBL have tested the system and recommend it. IBL now offer the system with their machines.
Real-time telemetry
Another technology that had to be investigated was real-time telemetry that could reliably function within the vacuum stages of the process. For this type of process, engineers like to see the profile in real-time. This is tricky in any industrial machine as the RF energy is greatly attenuated by the metalwork etc. When there is a vacuum stage it is even more difficult, as it is essentially a sealed metal box, we rely on wiring etc. through into the chamber to allow any RF energy to be in/out.
SolderStar’s approach is innovative and has proved an exceptional solution. The system is designed using ‘mesh networking’ technology which provides a ‘self-healing’, very reliable, network/data link. The approach allows routers/repeaters to be used as necessary to relay the signal in machines where other systems would simply not work. Normally no repeater is necessary if the PC receiver is within 10 meters of the machine. Additionally, as no signal is 100% guaranteed they employ an intelligent ‘2 way‘ protocol, if a ‘dead spot’ is encountered for a few seconds in the machine, the datalogger buffers the data then offloads once the link is re-established catching up and continuing in real-time. Other systems just miss the data.
Conclusion
Vapour Phase soldering has become competitive for high volume productions. State-of-the-art machines offer high throughput in combination with high quality results. The vapour, like all gases, is tending to equally fill out a given sphere, such as a Vapour Phase process chamber. The equal temperature distribution over the boards is automatically provided by this physical effect, while in a convection oven the cross profile can vary in temperature. The physical limitation of the maximum temperature in a vapour phase system does not require further controlling mechanisms to avoid overheating. This quality feature is also today providing the highest benefits in long-term reliability of the soldered electronic boards. In a convection oven the creation of temperature profiles needs thorough preparation, overheating cannot be securely avoided especially on boards with varying mass distribution.
The excess heat needed to ensure a perfect solder result in vapour phase soldering is only 5°C to 10°C over the melting point of the solder paste. Other reflow methods require 30°C to 35°C excess heat for the same task due to its lower heat transfer rate.
Lower soldering temperatures are limiting the stress for the components, avoid delamination on PCB substrates and limit the risk of popcorning on modern components. The vapour phase process provides an oxygen free atmosphere at no extra cost leading to the best possible wetting. The energy consumption (typically 5-6 kW for a large inline system) is much lower than convection as the energy remains in the hot liquid. Optimised insulation reduces the introduction of heat into the surrounding and thus enables to save air conditioning cost in the plant. Vapour Phase ovens are smaller than convection ovens, thus they also save space in production. Considering today´s and future complex components and processes, vapour phase is a perfect choice, and together with SolderStar profiling system and its dedicated software, it allows vapour phase machines to be defined, enabling the process to be controlled to the same extent as conventional reflow oven.
Information used from:
www.asscon.de
http://www.rehm-group.com
Views
Skyscraper 1
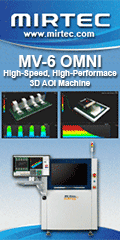