One of today’s major cleaning challenges is to successfully clean and rinse under bottom terminated components. Because of the demands placed on modern printed circuits, including increased component density and circuit complexity, cleaning proves especially critical to ensure proper reliability.
This article examines the interplay between cleaning agent and number of rinse cycles on the resistivity of the rinse water, the ionic contamination on the board, and the relative amount of organic residue present in the rinse water and trapped under bottom terminated components. By understanding the nature of these interactions, the ability of different cleaning agents to be rinsed and the optimum rinsing protocol for aqueous cleaning agents can be determined.
In an aqueous electronic assembly cleaning process, water quality is extremely important. Water purity at each process stage, low levels of foam, applied impingement energy, rinse temperature and rinse time are critical factors to ensure an adequately rinsed part. An inadequately rinse part can leave behind residue that may impact product reliability.
Rinsing Study
The commercially available aqueous cleaning agents in this study are commonly used in cabinet style batch cleaning machines. The properties of the seven cleaning agents are categorized within Table 1. The letters within the table mean the following: CA = Cleaning Agent; H = High; M = Medium; L = Low.
Table 1: cleaning agents included in this study
Process parameters:
- Wash time: 5 minutes
- Wash temperature: 65°C
- Rinse temperature: 26.6°C
- Number of rinses: # needed to reach value
- Resistivity setting: 250kΩ and 500kΩ
The cleaning agents were run in a cabinet style batch cleaning machine. The circuit boards processed within the machine were pre-cleaned to ensure that no flux residues were present under the chip caps. The purpose of the pre-cleaning was to eliminate the interference from residual anions or cations present in flux residues that may remain after cleaning and to ensure that these ions do not skew data findings. The research objective was to compare rinsing effectiveness on industry-accepted aqueous cleaning agents.
For the batch cabinet cleaning machine used to run the DOE, a rinse cycle added approximately three gallons to the process chamber at ambient temperature. No heat was added to the rinse water before the rinse cycle was initiated. Each rinse ran for 30 seconds. Following each rinse, a mid-stream sample was collected as the water was drained. A chemical oxygen demand (COD) analysis was run on each water sample collected.
The quantitative study researched the rinse efficiency of each cleaning agent. The rinse efficiencies were measured in the following five ways:
1. A wash cycle was run with no boards loaded into the cleaning chamber. The number of rinses needed to meet rinse water resistivity values of 250 kΩ and 500kΩ was determined.
2. The machine was loaded with 15 clean Kyzen low-gap test vehicles. Boards were pre-cleaned to ensure no flux residue is present under chip caps. After that, a wash cycle was run but a water rise following the wash was not run. Two boards were collected, air was blown off, the boards were bagged and ion chromatography (IC) was run.
Figure 1: Board Configuration – Yellow boards are the sites where the boards were taken for IC analysis
3. The machine was loaded with 15 clean Kyzen low-gap test vehicles. A wash cycle was run and the number of rinse cycles needed to achieve 250kΩ water resistivity was determined. Two boards were collected, air was blown off, the boards were bagged and ion chromatography was run.
4. The machine was loaded with 15 clean Kyzen low-gap test vehicles. A wash cycle was run and rinsed to 500kΩ water resistivity. Two boards were collected, air was blown off, the boards were bagged and ion chromatography was run.
5. Following each rinse cycle, a sample was pulled at the drain line to run a COD analysis in mg/liter. A mid-stream sample was pulled after each rinse and a series of COD measurements were run for each cleaning agent tested.
Data Findings
Test #1: A wash cycle was run with no boards loaded into the cleaning chamber. The number of rinses needed to meet rinse water resistivity values of 250kΩ and 500kΩ was determined.
Figure 2: Number of rinses needed to meet set values
The batch cabinet cleaning machine automatically determined the number of rinse cycles required based on the resistivity of the rinse water during each rinse. The rinse cycles needed to reach the preset values were relatively similar with the exception of cleaning agents with lower pH values. The data found that one additional rinse cycle on average improved the resistivity value from 250kΩ to 500kΩ.
Test #2: The machine was loaded with 15 clean Kyzen low-gap test vehicles. A wash cycle was run but the boards were not rinsed following the wash cycle. IC was run on the boards to measure the cation levels present following a wash cycle. Figure 1 illustrates the placement of Boards #1 and #2.
Figure 3: Legend for IC data
Figure 4: Cation levels before rinse. See Figure 3 for legend.
Many aqueous cleaning agents use amine activators to saponify and soften rosin and resin structures. These amines are derivatives of ammonium cations, and as such can show on IC as ammonium. To avoid disclosures of proprietary amines, no effort was made to identify or quantitate amines — they were treated as ammonium for the calibration of the IC. The anticipated response differences between various common amines were small enough to allow for relative comparisons instead of absolute comparison. Cleaning agents that are highly buffered resulted in lower levels of the ammonium ion. CA-1 registered high ammonium ion levels, indicating a cleaning agent that is poorly buffered and containing higher levels of free alkalinity. Magnesium, sodium, potassium and calcium were found at higher levels from some cleaning agents vs. other cleaning agents.
Test #3: The machine was loaded with 15 clean Kyzen low-gap test vehicles. A wash cycle was run. Following the wash cycle, the number of rinse cycles needed to reach rinse water resistivity of 250kΩ was tabulated. For each rinse cycle run, a sample was pulled for COD analysis. Once the rinse water reached 250kΩ resistivity, the rinsing process was stopped and two boards were collected for IC analysis.
Figure 5: Cation levels at 250kΩ. See Figure 3 for legend.
The cation levels present at 250kΩ showed mixed results. The ammonium ion for CA-1 was reduced by a factor of 5:1 vs. not being rinsed, yet was unchanged on CA-2, CA-5 and slightly increased on the others. Upon rinsing, the ammonium ion hydrates and hydrogen bonds with water, resulting in a potentially higher recorded level. While reduced, CA-1 with low buffering remained at consistently higher levels of ammonium ions vs. the more buffered materials. One of CA-4’s cards showed an increase in ammonium, sodium and magnesium while calcium did not have a large spike like the un-rinsed condition. Overall, rinsing to a value of 250kΩ did not show a significant change in ionic contamination vs. no rinsing except on the less buffered cleaning agent.
Test #4: The machine was loaded with 15 clean Kyzen low-gap test vehicles. A wash cycle was run and the number of rinse cycles needed to reach rinse water resistivity of 500kΩ was tabulated. For each rinse cycle run, a sample was pulled for COD analysis. Once the rinse water reached 500kΩ resistivity, the rinsing process was stopped and two boards were collected for IC analysis.
Figure 6: Cation levels to 500kΩ. See Figure 3 for legend.
The cation levels present at 500kΩ rinse water were very low. The ammonium cation again remained higher for CA-1. The data found all the cleaning agents rinsed well relative to typically accepted values. Cleaning agents with higher pH values and greater alkalinity required 1-2 additional rinse cycles. Compared to the 250kΩ results, one additional rinse typically was required to achieve the 500kΩ value, providing consistently lower ionic values.
Test #5: Following each rinse cycle, a mid-stream sample was pulled at the drain line to run a COD analysis. The purpose of this test was to provide a rough indication of the amount of bulk organics, presumably cleaning agent, in the rinse water for each rinse.
Figure 7: COD measurements on each cleaning agent for each rinse cycle. Note the logarithmic scale.
The COD levels were measured for each rinse cycle. The first rinse cycle recorded the highest COD level, which indicates that the majority of the wash solution was removed using the first rinse cycle. During the first rinse, the organic constituents within the cleaning agent contributed to the COD level. CA-2 was run at 25%, with the data bearing out that during the first rinse sample, the COD levels were higher. On some cleaning agents, the COD levels were very low, indicating a cleaning agent that wets and drains from the assembly and wash chamber well following the cleaning process. The COD values ranged over several orders of magnitude so a base 10 logarithmic transformation was used. Following the first rinse, the COD levels dropped significantly, which indicated that all the cleaning agents were rinsed well with water.
Conclusion
The data finds that all the commercially available cleaning agents in this study are highly rinsable with water. The bulk of the cleaning agent left on the boards and within the process chamber is rinsed off the assembly during the first rinse cycle. The subsequent rinse cycles effectively remove trace ions and cleaning agent remaining on both the assembly and within the process chamber.
The data finds that the ammonium ion is more pronounced on highly saponified/less buffered cleaning agents. This strength of the buffer also can be a contributing factor to the ammonium ions present. On highly buffered cleaning agents, the ammonium ion dissociates when rinsed and has a higher tendency to be detected.
The data finds that 4-6 rinse cycles are needed to reach water resistivity of 250kΩ. To reach 500kΩ higher purity levels, only an additional 1-2 rinse cycles is required. The additional rinse required to 500kΩ made a notable change in the level of ionic species detected.
The effect that the number of rinse cycles has on the organic materials in the rinse water varies more than the ionic data. Some cleaning agents had an approximate 98% reduction in organics after the first rinse, while others took additional 3-4 rinses to achieve that reduction. This presumably arises from the wide variety of organic materials used in cleaning agents. Some organics are highly water soluble and will be removed at a faster rate than less soluble ones. Because the COD data is a non-specific, it will vary more than a specific test. This is because the fundamental properties of ions are relatively constant, so sodium ions will all have similar solubility properties regardless of cleaning agent type, whereas the shear variety of organic molecules in aqueous cleaning agents mean that some will leave at faster rates than others.
Acknowledgements
The authors acknowledge Kevin Soucy and Chelsea Jewell for their work in setting up the cleaning equipment, building test vehicles and running the DOE. The authors also acknowledge James Perigen, Jacob Thomas and Haley Jones for this work in running the IC and COD analysis.
For more information, contact David Lober, Dr. Mike Bixenman, Ram Wissel and Jason Chan at Kyzen Corporation, 430 Harding Industrial Drive, Nashville, TN 37211; Web site: www.kyzen.com.
Skyscraper 1
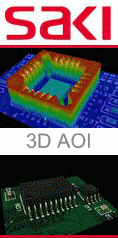