The third dimension is an increasingly essential aspect of AOI. Today, the decisive factors in 3D inspection include true-to-life representation from all selectable viewing angles, first-class throughput strengths, exact, certified 3D measurement and multiply networked data exchange.
Modern 3D technology is now an indispensable element in automatic optical inspection of electronic assemblies. The three-dimensional back calculation of assembled printed circuit boards is more and more precise; thanks to improved resolutions and faster technologies, more and more data are available for evaluation. As a result, height information can now be taken for granted. This is attributable to the well-proven fringe projection method: Calculating the position and height of any point on the electronic assembly requires the unequivocal back calculation of projected patterns. One or several projectors map the printed circuit board through an overlaid pattern of stripes in grayscale values. To obtain distinct average values, three phase shifts of the projected pattern must be acquired from each of at least two perspectives. The more perspectives are used, the more reliable are the measurements, for example, because shadowing from tall components no longer has a disruptive influence. Projection of the stripes, or pattern, takes various forms. Numerous narrow stripes serve to improve the resolution of the depicted object. In turn, wide stripes enlarge the possible measurement area. The exact spatial positions of the individually measured points are determined by means of a triangulation process.
Different hardware concepts
One well-known approach in 3D AOI is the use of just one orthogonal camera. To build up a three-dimensional reconstruction, four or eight (for example) projectors set at an angle cast successive stripe patterns over the centrally positioned inspection object. The camera uses the information gained thereby to calculate the spatial images. Viscom has already taken a high-value approach here for decades, which pays even greater long-term dividends when seen against the backdrop of progressive technological development: Only one projector is needed in the Viscom 3D inspection systems because in addition to the orthogonal camera, four or eight laterally attached angled cameras can be selected (Figs. 1 and 2). This results in terrific advantages where speed is concerned, since several images can be acquired at the same time. For instance, if 64 images are acquired to accurately capture a scene, with eight side cameras, they can be acquired for all the necessary stripe patterns in 16 time slots instead of 64. If a lower resolution is adequate for the inspection, eight simultaneous acquisitions instead of four are also possible. In this process, the projector functions similarly to a beamer and can quickly and dependably generate all necessary forms and patterns. With this approach, the criteria of inspection speed and quality can be versatilely implemented to meet requirements.

Figs. 1 and 2 Comparison of image acquisition methods: conventional approach with an orthogonal camera and the Viscom approach with four side cameras
Ensuring measurement accuracy
One of the central aspects of final inspections in electronics manufacture is determining whether or not deviations from the specified ideal values are still within an acceptable tolerance range. In the automotive application field, for example, the increasingly smaller LEDs used in headlights and other vehicle lighting have very strict requirements for positioning. Precise assessment of defects such as minimum tilting depends on reliable measurement values. It should be possible to test the measurement devices against a certified target. This permits verification of the repetitive and absolute accuracy of the 3D AOI. The certified target Viscom offers for this purpose is an exactly manufactured height gradation, which was measured with high precision instruments by a specialized laboratory.
Because their forms have particular features which must be taken into account, special criteria apply for solder joints. Additional factors here include dealing with disruptive reflections, or component bodies such as chips, which may conceal their own solder joints. According to Viscom’s experience: To calculate, say, the volume of solder joints and exclude errors in the process, having as many side cameras as possible is advantageous.
MCS and meaningful height profiles
In principle, an approximate measurement of the solder joint is already possible with the outermost lower and the topmost point of the meniscus. Viscom takes a more advanced approach, where a very accurate height profile of the solder joint is reproduced on the basis of numerous individual points (Fig. 3). Yet another important value is determined during the measurements: the minimal cross section (MCS). This value is the shortest distance between the surface of the meniscus and the component’s base. The MCS is the most probable location for wear and overload to result in crack formation. Viscom has integrated solder joint measurement into the software versions vVision 2.4 and SI 8.4. Inspection system operation, particularly with vVision, is extremely simple (Figs. 4 and 5). This is true both for creating and optimizing an inspection program as well as handling the inspection library. Even inexperienced operators quickly arrive at good results.

Fig. 4 Example of the inspection properties in vVision: The expected volume of the component type is displayed for comparison. The overview at the right of the image explains the process step.

Fig. 5 The measured height of approx. 1500 µm along a superimposed profile is displayed (inspection properties in vVision).
Stronger throughput with XMplus camera technology
The data amounts necessary for three-dimensional considerations and evaluations are significantly greater than for 2D and 2.5D. Especially with the XMplus camera module from Viscom, extensive inspection depth and very low cycle times are no longer mutually exclusive. Technology directed toward high performance provides an image data rate of up to 3.6 gigapixels per second. The field of view measures 50 by 50 mm, while inspection speed is up to 65 cm2/s. This accomplishes an ideal relation of high throughput and high resolution. Even 03015 components can be inspected with full reliability. An especially powerful frame grabber was conceived for the XMplus camera module and the control software was adapted to the increased requirements. One measurement point every 10 µm can be used to determine exact values. The z-resolution is 0.5 µm, facilitating exceptionally precise height calculations. In this process, the component heights can be up to 25 mm. The XMplus camera module is a standard series component of the S3088 ultra gold 3D AOI system (Fig. 6). The well-proven Viscom FastFlow Handling transports inspection objects at high speeds, with electronic assemblies cycled in about 2.5 seconds.
True-to-life 3D display
The side cameras in the 3D AOI systems offer another significant advantage alongside higher acquisition speed: The individual components can also be displayed in three dimensions with very realistic detail. This is made possible by Viscom’s new software advancement, 360View (Figs. 7 to 14). The operator selects the best viewing angle for the specific task and always receives an optimally textured image. When this new image quality is compared to conventional acquisitions, it is apparent that in the latter, the sides of components are often displayed with waterfall-like imprecision. Why? Only the superimposed information from an orthogonal camera is available. In contrast, thanks to the optimal application of side cameras, 360View enables a true-to-life 3D display from practically all unobstructed viewing angles, ensuring secure defect classification.

Fig. 12 Incorrectly placed MELF component (metal electrode leadless face); 3D display with 360View in vVision
Industry 4.0 in the production line
When implementing concepts within the scope of Industry 4.0, 3D inspection systems for SPI, AOI, AXI and MXI from the same source are an obvious advantage. With the Quality Uplink software feature, Viscom enables intelligent linking of results from the different inspection gates (Fig. 15). The operator has fast access to all the essential data and images (Fig. 16). Comprehensive defect assessments are significantly more convenient and processes can be more effectively optimized. Now, Viscom even offers an open interface to SPI systems from other manufacturers. In concrete terms, this means that a customer who has decided on a 3D AOI system from Viscom can also combine its results with those from a solder paste inspection for a networked evaluation, even if the SPI system is not from Viscom. Furthermore, the inspection systems can carry on fully automated communication with, for example, the placement machines and paste printers, and influence their parameters (Closed Loop).

Fig. 15 The 3D AOI systems from Viscom are intelligently networked in the production line. This is ensured by the Viscom Quality Uplink software feature, which enables connections to the paste printer and placement machine (Closed Loop).

Fig. 16 The results of different inspection gates in the Viscom Uplink Process Analyzer (VUPA), SI platform
On the verification stations vVerify (vVision) and HARAN (SI/EasyPro), networking can now extend far beyond a single production line. Usually a special software provides local support to the operator in verifying the automatically detected defects, using images of good and bad examples to prevent human error. Nowadays, however, verifying results from inspection systems in several lines can be consolidated to a single workstation. Production and classification can thus be carried out across locations and even countries that are spatially separated from each other. One of the advantages is that an experienced employee does not need to be on location to accomplish the essential verification tasks. Impressive results to support this goal can be achieved especially with the 360View concept described above.
Call up data from anywhere
Viscom places additional, systematic emphasis on practice-oriented use of the possibilities modern smartphones offer. As of vVision release 2.4, mobile real-time access to all important information of the inspection process is available via a Viscom app (Fig. 17). Generally, the retrieved data are maintained on a local production operation server. Key figures and diagrams are only a few clicks away. To develop solutions, responsible persons can reach the required data anytime and from anywhere. With the barcode scanner function, a smartphone camera allows immediate identification of each electronic assembly; its associated information is ready immediately.
Versatility with selectable inspection methods
Modern 3D inspection systems provide a free selection between all inspection processes and concepts, from 2D through 2.5D to 3D, to meet the specific requirements. Thus, 2D processes are still the ideal inspection method in areas such as OCR (optical character recognition) or to inspect for correct polarity. Relevant features are emphasized with the appropriate illumination, eliminating disruptive effects. To detect certain defect types, however, a view from above alone is not sufficient. In modern practice, 2.5D inspection has established itself in inspecting QFNs (quad flat no leads packages) and other applications. Especially where X-ray is unavailable, a reliable inspection can be performed with the angled views based on laterally attached indicator solder joints.
However, if it is necessary to ensure that a component is actually level on the printed circuit board (coplanarity) or the leads of an integrated circuit (IC) are not defectively bent and therefore raised (lifted lead), today 3D AOI is clearly the better choice. Also, component bodies are increasingly miniaturized and can be inspected more reliably with this method. In practice, today it comes down to applying the right combination of automated processes. Experience demonstrates that when 3D AOI is involved, first pass yield can climb relatively quickly from 80 to 90 percent. At Viscom, all inspection methods are embedded in a future-oriented concept of intelligent networking and the most up-to-date quality assurance.
Views
Skyscraper 1
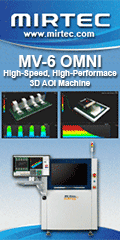