By Shupha Varghese, Business Development Manager
Founded in 1998, Optimal Electronics Corporation was established to deliver advanced production optimization capabilities for electronics manufacturers. Designing solutions for world-class manufacturers such as Rockwell Automation, Continental, National Instruments, Magna Electronics, Rockwell Collins, 3M, BAE Systems, Banner Engineering and Digi International, etc., Optimal Electronics developed integrated MES solutions that enhance the return on investment in plant and equipment by enabling greater manufacturing throughput and overall product quality.
Optimal Electronics’ mission is to increase the profitability of its customers by maximizing production efficiency and output, while reducing overall costs. Founder and CEO Ranko Vujosevic said, “We accomplish this by controlling and tracking the essential manufacturing data and processes through the use of a plant-level or company-accessible database.” Users control the entire manufacturing shop floor from their desktops or check status via dashboards on plant PCs or from tablets. He added that Optimal Electronics provides customers with a comprehensive software system that is simple to use and integrates manufacturing data with ERP/MRP systems.
One of the major changes impacting the electronics assembly process is the increasing market demand for detailed component-level traceability throughout each stage of the assembly process. Managing the myriad of complexities involved in achieving accurate component traceability, at the most detailed level, requires an automated, cost-effective approach for meeting customer expectations, while minimizing costs, human intervention and headcount.

Optimal Electronics’ Optel MES solution provides a fully integrated, mobile, modular shop floor control system for productivity improvement, materials management, traceability and quality management.
Today’s electronics manufacturers need modern technologies and processes for managing and improving all aspects of the assembly environment – to overcome complexities, respond to changing market demand, and increase profit margins. Achieving these goals requires comprehensive, integrated, advanced MES capabilities that ERP/MRP systems, machine vendor software, and most MES vendor solutions do not provide. Optimal Electronics’ Optel MES solution delivers unique functionality and resulting benefits.
Optimal Electronics’ Optel MES solution provides a fully integrated, mobile, modular shop floor control system for productivity improvement, materials management, traceability and quality management.
The company’s powerful Optel solution provides complete capabilities for accurate work order level, panel level and component circuit level traceability by interfacing directly with SMT placement machines on the production line. Optel enables online setup verification to be fully automated, ensuring that the correct parts are loaded into the correct SMT machine slots. With the Optel system, manufacturing operations also can leverage automated capabilities for real-time component cycle counting and advanced parts outage warnings to significantly reduce machine downtime and increase production output.
One of Optel’s most significant advantages is its innovative Optimized Dynamic Scheduling technology, which is key to competitiveness and profitability in a high-mix, low-volume environment. Unique to Optel, this technology drives major increases in production and utilization without the addition of new SMT equipment. No other software on the market today enables the optimization of production capacity that can deliver up to 50 percent increases in production, 80 percent reduction in changeovers and 50 percent reduction in changeover duration.
Optel’s Optimized Dynamic Scheduling approach uses selected business rules and advanced algorithms, at three levels, to increase production by automatically generating optimized clusters of work orders and creating SMT machine programs. Unlike static software grouping approaches, this technology re-optimizes production schedules dynamically, as new work orders enter the production stream.
Benefits
Optel is a complete manufacturing execution system, built around a single centralized database, that provides the full range of integrated functionality needed to effectively control, monitor and manage all phases of the electronics assembly process, including:
• Materials management: inventory and warehouse management, materials tracking throughout the plant, and materials serialization; MSD control, bar code data collection.
• Dynamic scheduling: dynamic scheduling of work orders into common setups as work orders are released, optimization of setups, priority criteria selection, with lean kitting to support grouping.
• Pre-production control: kitting, offline and online setup verification, feeder management, and work-in-process tracking.
• Materials traceability: from the work order level to the circuit level and to the final assembly level.
• Process traceability and control: process definition and enforcement, multi-level routing, full process traceability, verification and data collection across the production facility.
• Component traceability: instant access to date and lot code information for every component within a work order; serialization option enables the identification of components installed, per reference designator, on individual circuit assemblies.
• Quality management: quality data and defect data collection from inspection stations and automated equipment; support for rework repair and returns processing.
• Graphical documentation: provides paperless, database-drive, graphical work instructions for box-build, circuit assembly, rework and for QA inspection. It allows assembly instructions and multimedia content to be assigned to assemblies either at the component level or at the assembly level.
• Machine Performance Monitoring: monitors machine downtime by shift, day or week; track number of feeders setup for next setup; monitor ideal/actual cycle time, machine efficiency, OEE and utilization.
In addition to these capabilities, Optimal Electronics can customize Optel to fit customers’ unique manufacturing environments, processes and requirements.
Smart Factory Software Solutions

Latest addition to the Optel software suit is control of sensor assembly in clean rooms, including setup verification, die attach assembly, wafer packaging, component traceability and process control
Latest addition to the Optel software suit is control of sensor assembly in clean rooms, including setup verification, die attach assembly, wafer packaging, component traceability and process control
In recent years, Optimal has expanded its product suite to offer software solutions for sensor assembly in clean rooms and Smart Factory (Industry 4.0) solutions. Although its core will remain dynamic production scheduling and MES solutions for some time, Optimal is moving high speed into Industry 4.0. Optimal recently hired a robotic expert to work on new Industry 4.0 projects. Vujosevic said, “We are working on several Industry 4.0 projects now, involving intelligent machines, intelligent process control, automated material replenishment, self-scheduling assembly lines, etc. All of these projects include artificial intelligence and robotic applications. Everything new we develop is for mobile applications. Our customers now can monitor the entire plant operation and board by board production on each line on their cell phones and other mobile devices.”
International Expansion
Optimal Electronics is in the midst of an international expansion. The company signed a reseller agreement with ETEK-Europe for sales in Europe. Optimal will open a support and development office in the Republic of Montenegro in early 2018. Optimal also signed distribution agreements for South East Asia and China, and it will open its first Asia office in the Shanghai Free Trade Zone by the end of 2017. “We are very excited about our expansion in Europe and Asia. We have customers in Europe, Malaysia, Singapore and China and want to use those references to expand our customer base,” Vujosevic added. “We also are increasing our marketing reach to enhance our brand recognition. Additionally, there is much interest in Smart Industry 4.0 Software solutions in Europe and Asia that we currently do not find in the United States.” Optimal will continue aggressive direct sales in the USA and Mexico, and plans to open an office in Monterrey, Mexico, in Spring 2018 to support new customers and increase sales efforts throughout Mexico.
For more information about Optimal Electronics Corp., contact Ranko Vujosevic, Ph.D., CEO and CTO at 13915 Burnet Road, Suite 312. Austin, TX 78728; 512-372-3415; Email: ; Web site: www.optelco.com.
Views
Skyscraper 1
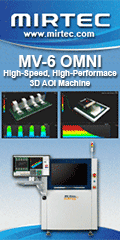