By Gail Fao, Business Development Leader, Energy Focus
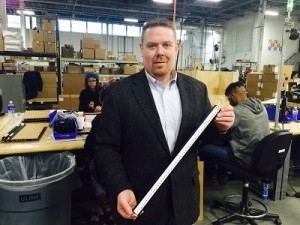
Jason Deist-Director of Operations, holds a 2 ft. LED assembly that is being furnished to the US Navy.
Headquartered in Solon, Ohio, Energy Focus is a leader in tubular LED lighting and strives to enlighten and inspire not just its customers but the entire industry. The company provides energy-efficient LED lighting products, and develops energy-efficient lighting technology. Its solutions provide energy savings, aesthetics, safety and maintenance cost benefits over conventional lighting.
Energy Focus’ vision is to be the trusted leader in LED lighting retrofit, and the plan is working. In 2012, the company had six assembly employees, but by 2015 that number had grown to more than 70. By the end of the second quarter of 2016, Energy Focus’ main facility will expand to 116,000 sq. ft., with all the processes done using lead-free technology.
Jason Deist-Director of Operations, holds a 2 ft. LED assembly that is being furnished to the US Navy.
The company is proud of its long-standing relationship with the U.S. Government, including numerous research and development (R&D) projects for the DOE and DARPA, creating energy-efficient LED lighting systems for the U.S. Navy fleet. Customers include national, state and local U.S. government agencies as well as Fortune 500 companies, the U.S. Navy and many others. Energy Focus specializes in designing, development, manufacturing and marketing energy-efficient LED lighting, and has years of experience in retrofitting hospitals, government buildings, schools and the U.S. Navy fighting fleet.
As part of the U.S. Navy’s “Buy America” mandate for ships as well as the Department of Defense’s desire to meet the “Buy American Act” with its shore base facilities, Energy Focus wanted to find a way to manufacture both 2 ft. and 4 ft. LED printed circuit boards (PCBs). Currently, the majority of these boards are made in other countries, but Energy Focus’ strategy was to be one of the first companies in The United States to manufacture these, making LED lighting fixtures competitive with offshore companies. To accomplish this lofty goal, however, the company needed a trusted, experienced partner and a line of top quality, advanced technology systems.
Jeremiah Heilman, Vice President of Research and Development at Energy Focus Inc., contacted David Trail, principal of Horizon Sales, a leading manufacturers’ representative corporation that specializes in the sales and marketing of premier electronics assembly equipment, to get the ball rolling. Over an informal meeting, the men drew up plans for printing 4 ft. boards onshore. The line that Energy Focus wanted to build would need to be fully automated and it would need to be capable of producing 1 million LED assemblies per year on one shift. That was a tall order.
Trail went to work designing the line with his team, knowing that only the best, most reliable and advanced technology systems could be on the line. Nothing like this had been built in the United States before so there was no standard to turn to – he was charting new territory. Trail included systems from Juki Automation Systems, PROMATION Inc. and Viscom. He submitted his $1.5 million design to Jason Deist, the company’s Director of Operations, who, in turn, brought it to Energy Focus’ board of directors. The design was approved and in early September 2015, the equipment was ordered. Energy Focus was going to have the first fully automated LED assembly line of its kind in the United States.
In order to compete with China and other Asian countries in assembling 4 ft. LED boards, the process had to be completely automated. The fully automated system allows faster and more cost efficient processes in comparison to manual labor.
On the appointed day, three truckloads of equipment was delivered to Energy Focus. Two days later, the line was successfully up and ready to produce as many as 1 million LED assemblies per year on one shift.
On the date promised, three semi-trucks delivered crates and crates of equipment to Energy Focus’ load docks. Riggers were hired to unload and uncrate the systems. After only two days, the entire 98 ft. automated line was not only up but it was running successfully and was assembling product. All the equipment worked together and there were no issues. Trail said the systems were taken out of the boxes, set up, powered up and green lighted. He added that he chose the systems he did because the manufacturers are known for quality, speed and consistency.
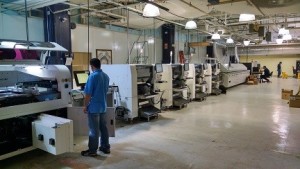
On the appointed day, three truckloads of equipment was delivered to Energy Focus. Two days later, the line was successfully up and ready to produce as many as 1 million LED assemblies per year on one shift
“What we did isn’t magic, it’s done every day,” said Trail. “The magic is that it was done on 4 ft. boards, and that the 98 ft. line was up and running in two days. In my 35 years in this industry, nothing of this scope or technology has ever happened before.”
In order to handle the boards and all the necessary machines, the line had to be no more than 98 ft. long. It is 100 percent automated and builds one 4 ft. PCB every six seconds. These fixtures meet Energy Focus’ goal of making LED lighting in the United States that uses one-third of the energy of florescent bulbs. The fixtures made on the line will replace the current 4 ft. fluorescent tubes and are all solid-state and all LED.
Emmil Makram (left), SMT Supervisor, and Deist hold a 4 ft. LED panel that consists of 10 separate LED PCBs. They are standing in front of the Juki/GKG PMax printer – which is only a few worldwide that is capable of producing 4 ft. panels in large quantities.
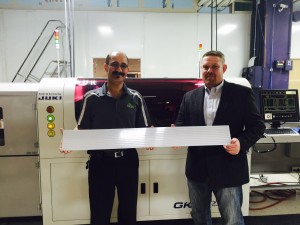
Emmil Makram (left), SMT Supervisor, and Deist hold a 4 ft. LED panel that consists of 10 separate LED PCBs. They are standing in front of the Juki/GKG PMax printer – which is only a few worldwide that is capable of producing 4 ft. panels in large quantities.
The line starts with a PROMATION board loader where the boards are set in as a stack. Suction cups pick up a board and place it on the PROMATION conveyor. From there, the board goes into the Juki/GKG printer, which is one of only a few that is capable of printing boards that long.
Then the PCB moves to a transfer conveyor and into the Juki pick-and-place, which places 65,000 components per hour (or half a million a day). This is a sequential pick-and-place process for a total of four machines. The board leaves those four placement machines and goes into a PROMATION inspection workcell, followed by Juki Automation Systems’ 10-zone oven. Juki partnered with JT Automation to provide a 10-zone convection reflow oven. Because the board is 4 ft., it needs all 10 of the zones. After that, the board is inspected by a Viscom S3088 automated optical inspection (AOI) system, where every component on the board is 100 percent inspected.
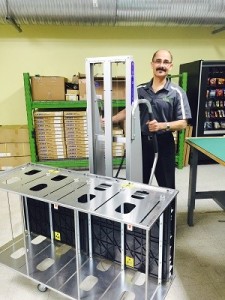
Makram using an Aluma Lift device to move around magazines from PROMATION Inc. that are automatically loaded with finished LED assemblies.
The AOI system is unique because it synchronizes the entrance and exit conveyors in order to accurately process the 4 ft. boards: the first third of the board is processed and exited while the middle third is brought in, and then the final third. The synchronization must be extremely accurate. Post-inspection, the board goes into PROMATION magazine loaders to stack. Because there are numerous boards, each one is slid into its own magazine slot to ensure that the boards do not touch but are still stacked. Each magazine can accommodate 50 panels, and there are four magazines (two on the top and two on the bottom) on the line. This was done to save space since Energy Focus only had a maximum of 112 ft length to dedicate to the line. Stacking the magazines reduced the needed amount of space from 16 ft to 8 ft. When the magazine is full, it is removed with the help of an Aluma Lift and from there the boards go to functional test and then into final assembly to be prepared for shipping. Each Makram using an Aluma Lift device to move around magazines from PROMATION Inc. that are automatically loaded with finished LED assemblies.
4 ft. board is slid into a clear plastic housing with white caps on either end.
LED lighting provides numerous benefits over florescent lighting, and Energy Focus wants to educate the industry about the technology’s benefits. The company believes that manufacturing these fixtures in the United States will place it in the unique position of being able to not only lead the North American industry but also to educate it. LED advantages include that the technology lasts much longer than fluorescent lamps, cuts energy costs significantly, are near indestructible and eliminates disposal challenges. Fluorescent lights lose 60 percent of their brightness in one year vs. LED lights’ six percent. Additionally, fluorescent lights give off substantial heat while LEDs emit far less. Unlike fluorescent lighting, quality LED lights are flicker free, which has been attributed as a cause of cataracts
Energy Focus continually strengthens its core capabilities and competitive advantages to ensure that it is meeting all of its customers’ needs while also preparing to meet the industry’s challenges of tomorrow. Its goal is to educate and assist clients in adopting advanced lighting products and solutions. To that end, the company develops, designs, tests and validates advanced LED products and solutions for its customers, while strengthening its global sourcing networks and capabilities. It provides clients with the most competitive, reliable products in the market in terms of time, quality, price, warranty and service. Energy Focus stands out from other companies because of its passion for developing LED technology that makes a difference in the world. This drives everyone at the company, from those in its production area to its sales teams. The proof is in the pudding: It is with this automated system that Energy Focus is one of the few – if not the only — U.S.-based company capable of producing one million LED lights per year on one shift. That’s making a difference one LED bulb at a time.
For more information about Energy Focus, Inc., contact the company at 32000 Aurora Road, Suite B, Solon, OH 44139; 440-715-1300; Web site: www.energyfocusinc.com. To find out more about the equipment used on Energy Focus’ line, contact David Trail at Horizon Sales, 3691 Honors Way, Howell, MI 48843; (800) 234-8688; E-mail: ; Web site: www.horizonsales.com.
Skyscraper 1
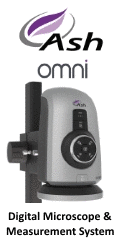