Advanced medical technology and robotic soldering: What are the requirements of medical electronics to support doctors?
Medical devices require exceedingly high quality and reliability due to their roles in prolonging human lives. Such devices are designed from specialty components and materials not typically seen in consumer electronics. Soldering to these components, which may be exceedingly small, made of exotic materials or that cannot tolerate flux presents a unique set of challenges often only suited to advanced soldering processes.
The importance of soldering in medical electronics
Health and medical treatments are advancing on a global scale. The life-sciences, medical and healthcare markets are constantly expanding due to technological progress and an aging global baby boom population. New devices are profoundly influencing human lives. These devices must be designed, developed and manufactured with the utmost care to ensure longevity and readability, especially in the most critical applications.
Many medical devices are becoming increasingly electronic in nature such as MRI and CT scanning equipment, medical endoscope, diagnostic equipment such as sphygmomanometers, and others. Medical devices are now considered highly qualified, reliable electronic products.
Designing and manufacturing these devices is sophisticated, requiring more specialized knowledge and experience to achieve stability and reliability of such electronics. One major cause of electronic device failure is poor solder joints between the components and substrate. Inappropriate soldering tends to cause such failures and disconnections. Thus, to provide reliable and accurate medical tools, qualified soldering is critical.
The nature of medical devices: Solutions with robotic and soldering knowledge
Soldering in medical devices can be broadly classified into two categories, both of which have stricter quality requirements than industrial and consumer electronics. The first, large diagnostic equipment such as MRI and CT scanners cost hundreds of thousands to millions of dollars. These devices contain extremely expensive PCBs and components due to their uncommon designs. Extremely high soldering quality is required and production quantities may be small. Therefore, as the demand for high quality grows, soldering operation is shifting from human to robotics.
The second category consists of medical devices that are in contact with or inserted into the human body such as pacemakers, catheters and gastroscopies. A large number of devices are distributed in the market and such products are small and precise. As a consequence, micro, fine or thin PCBs and components are used for production. The exceedingly small components are densely lined and mounted, making it almost impossible for hand soldering. Furthermore, medical device soldering is challenging because of the special metals involved.
Normal lead-free solder alloy has been standardized as a composition of tin, silver and copper. In the case of medical devices, however, the ratio of gold and silver is raised to impart special qualities such as strength and corrosion resistance. Needless to say, if the composition changes, it will impact soldering parameters such as temperature, wetting and forming. Meanwhile, the cost of solder alloy becomes expensive. Unless appropriate soldering processes are considered for special metals, the possibility of defect, failure and production costs are all increased.
Demands and requirements are varied in medical electronics soldering as previously described. To satisfy the diversity, manufacturers, who seek the most flexible and robust solutions, use robotic soldering. Robots, which excel at high-precision, repetitive tasks, are able to produce a consistent quality.
The method of laser also allows accurate soldering in narrow spaces without physical contact. Conventional contact soldering with tips is applicable for high thermal mass and for mass production. An ultrasonic method enables soldering without acid flux. Due to flux’s acidic activator, its usage in medical devices frequently is avoided especially if it will be inserted into the human body.
Therefore, ultrasonic soldering, without the necessity of flux application, has been gaining attention in the industry.
There are a limited number of operators with the skills to satisfy the strict requirements described above, and educating these experts is time consuming and expensive. As the skill of outstanding operators can be converted into robots, robotic soldering is seen as an effective manufacturing process, and its application among medical electronics manufacturers has become increasingly widespread.
Cavitation effect from ultrasonic sound waves
When ultrasonic vibrations are applied to a liquid, small bubble-shaped cavities are produced due to amplitude pressure differences. This phenomenon is called “cavitation.” The cavities are collapsed by atmospheric pressure, generating a large amount of energy. Ultrasonic soldering uses the momentary energy produced by cavitation to remove oxides on material surface.
In an ultrasonic soldering system, soldering is done with a heated iron tip that emits ultrasonic vibrations of 60 KHz. The ultrasonic waves generated from the oscillator are transferred to the soldering tip via a horn. The cavitation effect of the ultrasonic waves produces vacuum cavities (bubbles) at the interface of the substrate and the molten solder.
Recent RoHS directives and environmental regulations have resulted in the reduced use of flux or halogen, a material containing strong acids. The reaction layer (diffusion layer) formed during ordinary soldering also is formed in ultrasonic soldering after removing the oxide surface using the cavitation effect.
Global medical electronics becomes a bigger market
In terms of medical equipment, the United States market is more advanced than most. The majority of U.S. manufacturers produce large medical measurement devices, while general equipment is manufactured in factories in Puerto Rico, Dominica and other Caribbean countries. Products for Asian markets often are produced in Singapore.
On the other hand, outstanding medical electronics manufacturers can be found in Europe and Japan, which produce globally. Japan Unix is the global leader in robotic soldering with international sales exceeding 50%.
Japan Unix invests in world-class partners and soldering education
Process development and technical support are critical for robotic soldering. Japan Unix has established an extensive network of global partnerships to provide technical and sales support. Japan Unix invests heavily in these people and organizations to develop skillful experts for customers to rely upon for a high level of soldering support almost anywhere. Japan Unix works hard so its customers can enjoy world-class robotic soldering technology and a reputation of strengthening manufacturing competitiveness.
Wire-shaped products, such as catheters, are difficult to fix the position during operation, making them hard to solder. Japan Unix has established experts dedicated to developing special fixtures (jigs) for robotic soldering. The experts derive the best solutions from past or similar cases, and design fixtures that maximize productivity and robotic capability.
Japan Unix has established a soldering school to educate skillful engineers and soldering technicians that scientifically analyze soldering results. Additionally, the company has been appointed as the exclusive partner of IPC, the global standard for the manufacturing industry in Japan. IPC develops specialized standards for medical electronics due to its uncommon requirements. As a result, Japan Unix receives daily soldering sample requests from all over world, while meanwhile the company is working to maintain and expand “global standards.”
Skyscraper 1
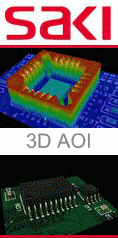