By MB Allen, Product Manager
A clear industry trend now spreading beyond the traditional North American and European markets is characterized by short production runs and frequent production line changeover. Improved technologies for line balancing, production planning, smart feeders, MES and more are being used more effectively to allow for faster production line changeover and less downtime.
One obstacle tends to be the reflow oven. Having a $2 million production line sitting for 30 minutes+ while waiting for a $40,000+ oven to stabilize on a new recipe will wreak havoc on profits. The goal should be instant oven changeover, and that goal is achievable in the majority of applications.
First, a few observations of the purpose of a reflow oven. I always ask process engineers the following question: What is the main job performed by the reflow oven? The answers tend to be to melt solder, solder the components onto the board and create a strong solder joint. All of that is true but there is more to it. Clearly, we do not want a strong solder joint that cracked the component in order to achieve it. So the reflow oven needs to solder the assembly within the tolerances/process window set by the relevant solder paste, components and substrate. The way we measure and control this is by the time vs. temperature profile of the solder joints, PCB and, most importantly, the components. In other words, the oven needs to produce the correct profile. We can even think of the reflow oven as a profile-producing machine.
A reflow oven has literally billions of alternative recipes. Each different set of zone temperatures and conveyor speed will produce a unique profile on a given assembly. It is imperative that the correct recipe is selected to establish the acceptable profile for all the different PCB assemblies. Therein lies the challenge. It may take an oven 10, 20, 30 or even 40 minutes to stabilize on a new set of temperatures, especially if the new recipe is cooler than the previous. (It takes longer to cool down an oven than to heat it up.) The key to instant or fast oven changeover is intelligent selection of the oven recipe. Clearly, if two different PCB assemblies are very similar and have the same process window, then it will be possible to select a single recipe that will produce an acceptable profile for both assemblies. An experienced process engineer can find such a recipe manually.
But what if the PCB assemblies are quite different in terms of size, thermal mass, etc.? This is a great challenge and it is not time-efficient to perform a trial and error experiment on billions of alternative oven setups to evaluate the resulting PCB profile for each in order to find a common recipe. But such a challenge is perfect for data mining using computers. Predictive software, even running on an old XP computer, is fast enough to do an exhaustive search on the recipes, and to select the optimal oven setup that will produce an acceptable profile for a wide range of different assemblies. This may seem complex, futuristic and expensive, but the fact is that several competing technologies have been able to do this for many years at low cost. The technology you chose, the applications you have and the reflow ovens you use will affect your success. For example, if you enjoy a modern oven with 10+ zones and you have a range of PCB assemblies that do not include the extreme low- as well as high-thermal mass, you may find a single recipe that can produce an acceptable profile for all your assemblies, hence the title of this piece: “instant reflow oven changeover.” The fastest oven changeover is no changeover.
In practical terms, one method to achieve this is to attach both the largest and lowest thermal mass PCB to the profiler and to run this train simultaneously through the oven. The data mining prediction software will select the correct oven setup only seconds after a completed profile. This is a simulated or predicted result so you are encouraged to verify the accuracy of the prediction by running a profile on the PCBs after the oven has stabilized on the new settings. Please note that this method also can be used when individual components on the same assembly have different process windows. The data mining software will search for an oven recipe that positions the profile inside every process window for every measured component on both PCBs. The probability is high that all the other PCBs that fall between the two extremes used for the recipe generation will have a profile in spec as well.
For a less capable reflow oven or a wider range of either thermal mass assemblies or process windows, there likely will not be a single oven setup that can handle everything. In that case, follow the same method described above, but narrow the grouping of PCBs. Users may end up with two recipes (small vs. large PCBs) or three or four groupings. In that case, there will be oven changeover delays, but limited to the few recipes there now are. Even in this case, it may be possible to eliminate or reduce the changeover time.
Prediction software or oven setup software allows control over the variables used for searching on the ideal recipe. For example, search on new recipes while allowing conveyor speed but not zone temperatures variables to change. Depending on the applications, it may be possible to get in spec on all or most assemblies simply by changing the conveyor speed. While an oven may take a long time to stabilize on new temperatures, the change in conveyor speed is near instant. To avoid the risk of making the oven the bottleneck in the throughput, limit the range of allowable conveyor speeds to a minimum speed that is faster than the rest of the line.
If the temperature must be changed in the oven, production planning should consider that an oven heats up faster than it cools down. It may be possible to start production with the coolest recipe and progressively go hotter throughout the production day.
Conclusion
It is not uncommon for high-mix electronics assembly factories to have more downtime due to changeover than actual production time. It is important to take a holistic view on the effect of production changeover for each production line as well as the entire operation. When drilling down to the individual machines, you may find that the biggest drag on your productivity is the reflow ovens. The use of more effective production planning and scheduling as well as modern data mining software to identify one or a few oven recipes may provide dramatic improvements to line changeover time and, consequently, profits.
For more information, contact MW Allen, Product Manager, at KIC, 16120 Bernardo Center Dr., San Diego, CA 92127; 858-673-6050; E-mail: ; Web site: www.kicthermal.com.
Views
Skyscraper 1
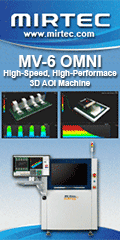