Highest Common Factor, not the Lowest Common Denominator,
Article By Michael Ford, Senior Market Development Manager, PCB Manufacturing, Mentor Graphics.
Using an advanced Lean new product introduction (NPI) methodology, as opposed to the traditional design-over the fence to-manufacturing flow, can enable companies that are involved in making electronic products to work together based on the highest common factor of functionality and opportunity.
A best-practice Lean NPI flow reduces the time-to-market for new products by enabling creation of a product design that includes real-world manufacturing constraints early on. In contrast to the lowest common denominator flow, an advanced, best-practice design-for-manufacturing (DFM) flow using a Lean NPI methodology begins at the PCB design stage and is incorporated throughout manufacturing, tying each stage much closer together. This more efficient flow is supported by the latest PCB design and manufacturing software from Mentor Graphics that enables communication of the design to manufacturing in a very efficient way, eliminating data reconstruction loops between the designers, fabricators, and assemblers. As a result, design re-spins and revisions can be avoided.
The seamless connection between PCB design tools and NPI manufacturing tools, as shown here with Valor NPI and Xpedition PCB Layout, enables an efficient best-practice Lean NPI flow.
This new DFM flow has to be able to ensure that the design satisfies the requirements of all areas of PCB manufacturing and assembly—quite a challenge considering the huge variation in companies that exists across the industry. Geographically, manufacturing operations vary significantly, from small tightly controlled operations in the west to more seat-of-your-pants mass production operations in the east, with pretty much every combination in between. The scale of manufacturing is quite wide as well, spanning the range from products in quantities of tens of millions where each may cost only a few cents to a single satellite controller that costs millions of dollars. Electronics industry sectors are also diverse: consumer, industrial, telecom, automotive, aerospace, and military, each with different priorities for cost, quality, flexibility, and delivery.
Electronics manufacturing services (EMS) companies operate across several sectors and tiers, as do original design manufacturers (ODM); this has resulted in a mess of different operations across the electronics manufacturing industry. And, each operation has the viewpoint that it is unique to the industry in one, or many, ways. Although this certainly could be the case, uniqueness is most often the consequence of evolution rather than intent, and much of the variation is probably no longer relevant.
In spite of these differences, however, when legacy practices are stripped away, the core of manufacturing is still pretty much standard—the technology of machines used is the same, the nature and supply of materials are similar, and the processes involved in the manufacturing operations match each other.
Thus, we can define best practices against these standard core values. One of the most important areas that needs a best-practice definition is new product introduction. The NPI process of taking an electronics-based product from design conception, through to manufacturing, and on to the final market to become profitable comprises essential standard common elements, no matter who, what, or where it is.
A best-practice Lean NPI methodology can be applied in virtually any circumstance. As an illustration, let’s take a look at two diverse examples of bringing a critical product to market, comparing the practices each one employed, following the companies’ transition to the Lean NPI flow, and then what they are able to do with the new practice. Through this process, we see how each fictitious but representative company brings differentiation and success to their product launch. Many companies in the market fall in between and around these two sample cases. However, all companies are capable of achieving similar benefits from the use of the Lean NPI methodology and associated tools, no matter how mainstream or niche their business may be.
Let’s Meet the Companies
The first company, which we can call “ABC Electronics,” is an example of a large established OEM company in the communications segment in Europe, with many manufacturing sites worldwide. The company’s core mission statement revolves around brand image, quality, and technology. Demand for increased flexibility as technologies progress around the globe is putting significant pressure on internal operations, with more product variations, shorter lead-times, and renewed cost consciousness. New competitors are coming into the market, driven by their local market demand for affordable technology.
The management at ABC Electronics wants to review existing internal operations, to create a potential doubling of capacity for new product introduction, and reduce overall costs. This has driven the need to look at identifying and removing needless duplicated operations and eliminating as much of the seemingly random human errors as possible, which cost production dearly.
The second company that we will look at, “XYZ Electronics,” is an example of a niche defence contract manufacturer (EMS), with just one manufacturing site based in California. This company prides itself on being able to make the highest possible quality in a very reasonable time at a very reasonable cost. The company’s core mission statement is to act strongly to win opportunities away from competitors and to grow strong, long-term, retained relationships with its customers. Responsiveness is also critical to provide a realistic price and delivery schedule in a timely way back to the customer, thus building confidence. Doing business in this way, however, has put extreme pressure on the process engineers who need to correctly identify any issues in designs that may compromise manufacturing quality, or business profitability.
The Companies’ Legacy New Product Introduction Practice
For ABC Electronics, the introduction of a new product follows a well-established internal flow. First, the design of the product, electrically and mechanically, is created to meet the required specification, followed by the layout of the circuit board, including selection of materials. The emphasis is on quality, cost, reliability, and performance. Manufacturing optimization is also a key consideration, even though issues with designs are said by the manufacturing teams to significantly increase costs for production.
Although a vertically integrated company, design and manufacturing in this company are not normally physically close, nor is the timing of manufacturing in line with the design cycle; this results in difficulty in getting useful communication going between design and manufacturing. The PCB layout designer is a specialist at what he does and has no knowledge or experience of manufacturing. He is measured on the performance of his designs and how designs are completed to schedule. Standard design rules within the design layout tool provide feedback for him in terms of general considerations of good design policy.
This process does not, however, include any significant qualification against manufacturing requirements. ABC Electronics’ legacy NPI process flow includes allowance for many re-spins, delays, cost, and call-backs. As well as lost time to create a new revision and repeating the NPI process, this annoys the designer who has already been working to a deadline for the next design, or even the one after.
In contrast, for XYZ Electronics, the NPI process is long, hard, and random/undefined. It begins with a sales team member bringing a USB stick of files from the customer. Very few of these are actually useful; and thus begins a long process of questions to the customer, who seems reluctant to reveal details about the product, even though there is a secure contract in place. The experienced NPI engineers put together their ideas of what the product is and how it should be made, continuously making assumptions, testing them against known features, and repeating. They interpret Gerber files, a graphical representation of the product, a file containing parts lists, and a simple bill of materials. With luck, these files will include placement locations. There can be some form of native CAD data included, which would be a pain to have to translate into several formats ready for process preparation on the different machines, but no time for that as yet. Significant work is required to put together all of these various pieces of information. It is a trial and error approach that nonetheless has to result in an error-free and low-risk product model. The sales team are already pushing for a response, wanting to show the best-in-service to their customer.
The XYZ Electronics sales team has a significant success rate in winning deals. The engineering team, however, with many specialists to cover the various types of machines from different vendors, spend significant time for each new product introduction to create the operational data for manufacturing. Unforeseen issues often come up, too late to be addressed with the customer, that simply have to be managed later. Additional production operators must be available and ready to deal with any situation. Quality and reliability of delivery cannot be threatened.
The Compelling Event
A shareholder report states that ABC Electronics needs to be more efficient if it is to stay competitive. Work starts to move around, with production being further optimized by locating closer to the customer, who needs more flexibility in supply with reduced finished good stock. Changes in production at different sites cause greater NPI work. Manufacturing engineers are less familiar with the types of products that they are suddenly expected to make and are challenged with the degree of flexibility that is being asked of them. There is no room in the NPI flow now for manufacturing-driven design re-spins. Design needs to be done right the first time, considering a vast range of manufacturing requirements, before it leaves the design office. The new Lean NPI tools are chosen to make that can happen.
For XYZ Electronics, the compelling event was a simple mistake, which caused the company significant embarrassment. An incorrect judgement in a sensitive product with a key customer had introduced unreliability in the product, found only after extensive life testing. Top management became very concerned that the error was simple and yet had been overlooked, while many products had been manufactured with a potential critical defect. The need to work with the customer and the cost of field support to test and rectify any issues exposed a key weakness in the manufacturing operation.
The decision to take control of the engineering data, to increase the ability of the engineering team to eliminate issues, and to give them time to completely eliminate the guesswork was clearly needed if the company was going to regain customer confidence. Adoption of a Lean NPI methodology and new software tools could make that happen.
The Lean NPI Methodology
Designers at ABC Electronics are now working with the Valor Lean NPI manufacturing software embedded in the Mentor Graphics Xpedition™ PCB Layout tool for PCB design. With this combination of tools, they can see opportunities to improve the design based on DFM analysis within the design tool itself. A few mouse clicks, and issues that would have caused manufacturing problems are eliminated.
Along with these changes, the seemingly endless complaints have stopped, because the DFM rules are refined continuously by a central manufacturing engineering team that represents sites from all over the world. The designer feels more productive and more satisfied as targets are now within his control to reach.
The Lean NPI methodology using a single, qualified product model throughout enables better and more efficient communication between PCB designers, fabricators, and assemblers.
The ABC Electronics central manufacturing team, responsible for both PCB fabrication and assembly, receive from design a single ODB++ (Open Database CAD-to-CAM data exchange format) file that contains all of the information needed for manufacturing, that is, the qualified product model.
This file is sent to the designated PCB fabricator, who loads the ODB++ file into the Frontline InCAM™ tools. The qualification of the product for fabrication has already been completed, so there is little to do other than simply start production once the machines have been set up.
For assembly, any new materials needed have been highlighted from design, with a complete physical model available from the Valor Parts Library (VPL). The data is ready to be sent to one or more production sites where the product is to be made. The qualified product model together with the parts library content means that there is very little preparation to do at each site. The local production bill of materials (BOM) is the only item that needs to be matched, which is done by the Valor Process Preparation tool, and this is followed by the direct assignment of product to potential machine and line configurations, providing choices for the planning team to optimize factory efficiency. Programs, data, and documentation are generated and sent to the machines as are other processes based on simulation of the operation, virtually eliminating the line trial and error down-time. The data for the machines is complete and fully detailed, including parts libraries in native machine format ready to load and run, all generated from the single library.
For XYZ Electronics, now that they are using the Lean NPI methodology, all data received from potential customers goes straight into the Valor NPI software. As part of the relationship with their customers, the sales people are encouraged to request that product information comes in the form of an ODB++ file, which professional design systems can easily output. The analysis of all of the data is now an automated procedure within the Valor NPI software, exposing potential issues that would otherwise affect manufacturing. As each issue is quantified, overall process operation can be determined to ensure the most accurate and risk-free operation.
Where there are issues exposed that manufacturing cannot easily cope with, they now have the opportunity to feed back the issues to the customer inviting them to improve the design in a collaborative way. This is an additional value from the EMS as a business, done in a way that promotes value to the customer rather than having to face difficult conversations once the damage has been done. When production is set up to build products, there is little additional work needed to get production up and running right the first time. An ODB++ file generated by the Valor NPI software is passed on to the Valor Process Preparation software, which then allows the creation of all the necessary programs, data, and documentation for any chosen line or lines.
Results from Using the Best-Practice Lean NPI Methodology
From a business standpoint, ABC Electronics now is able to introduce products across the world faster than ever before. The central team of process engineers are able to handle any amount of new products and variations in the market, and they have no issues when moving products from site to site to suit customer needs, production capacities, and efficiencies. Quality has also been enhanced, as inconsistencies between sites have been eliminated. The costs and delays associated with multi-site operation have been slashed. A far greater degree of control and flexibility has been achieved.
Business is also booming at XYZ Electronics, where new customers have been attracted by confident competitive pricing in a well-controlled and managed environment. Working collaboratively, the company has realized profit from the reduced risk of manufacturing issues, and its customers have benefited from better quality design with fewer related losses.
The best-practice Lean NPI methodology works for almost all companies, across the entire electronics manufacturing industry. The same tools within the flow, Xpedition, Valor NPI, InCAM, and Valor Process Preparation are all used to the extent required, and they are flexible to the context in which they are used. Opportunities continue to grow as OEMs work with CEMs using the best-practice Lean NPI flow as a standard platform and for increased communication, each company helping each other to be in control, and successful.
Companies Can Work Together based on the Highest Common Factor, Not the Lowest Common Denominator
In both scenarios, the software tools played their role to enable a much-improved design-to-manufacturing flow, delivering a strong result in each case. The Valor NPI tool especially played a different role in these scenarios. The software has built-in flexibility to enhance the design process, as part of the designers own environment where Xpedition is used, providing the ability to fully qualify the product before hand-over to manufacturing. Valor NPI also can be used by manufacturing as a tool to qualify designs and to identify opportunities for risk reduction through design improvement. The operation and result is the same, but for different people.
The value of a vertically integrated OEM is that the DFM operation using Valor NPI can be left-shifted into the design area. Within an EMS company, Valor NPI can actually be used by both parties, design and manufacturing, each for their own benefits. Collaboration between them is easier than ever before because of ability to collaborate with and share Valor NPI DFM rules. The Lean NPI methodology brings the highest common factor of functionality and opportunity, and not the lowest common denominator of flow that once needed to be used for these companies to work together.
This evolution of a best-practice Lean NPI methodology is a great deal more than simply creating a compelling case study. The key principles and tools for a the “highest common factor” best-practice allow companies to create their products in whatever way they choose and take them to market in whatever way they choose, while eliminating mistakes, waste, and errors. Successful new product introduction is achieved much faster, more reliably, with significantly reduced cost and improved quality.
About The Author:
Michael Ford is the Senior Marketing Development Manager, Valor Division.
Michael Ford started his career as a computer software and hardware engineer in 1982. Working for Sony in the UK, Michael became one of the first successful adopters of computer technology into the manufacturing shop-floor, going on to manage in Japan Sony’s global Lean Manufacturing solutions.
Joining Valor Computerized Systems in 2008 gave Michael the opportunity to apply his experience into the main-stream of the industry. With almost 30 years of experience, Michael’s key strength is the instinct of finding solutions and opportunities where there had been challenges and problems. Michael is currently working as part of the Marketing Development team within the Valor Division of Mentor Graphics, focusing on the realization of real and practical solutions for manufacturing based on the application of Lean Thinking, end to end, from design through the entire manufacturing process.
For more information about Valor, please visit www.valor.com
Skyscraper 1
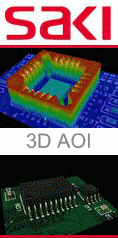