Saline Lectronics recently partnered with Cogiscan to implement their innovative Track, Trace and Control System throughout Saline’s 110,000 square foot manufacturing facility. Thoroughly committed to being a Solutions Provider in the EMS industry, this new system will allow Saline to offer customers detailed end-to-end traceability of product flow at every step of the manufacturing process.
As electronics technology advances to complex micro-components and to placing systems in harsh or human-critical environments, the need for thorough traceability during manufacturing is essential. Not only is this traceability necessary for the end-user to ensure that their product is safe and reliable, but it’s extremely helpful to the manufacturer in order to better regulate process and quality controls.
One of the most advanced solutions available on the market for EMS traceability is Cogiscan’s Track, Trace and Control (TTC) System. The TTC System provides visibility and verification of materials and product status throughout the entire manufacturing process – showcasing real-time data of work-in-progress, implementing a check and balance alert system to remove human error, and offering a history of component lifecycle and traceability in the event of a recall. Looking to provide the most comprehensive data to customers that require it, while also improving quality control throughout the factory, Saline Lectronics recently installed this TTC System in its static-controlled manufacturing facility in Saline, Michigan.
“Saline Lectronics chose to partner with Cogiscan for the Track, Trace and Control System in order to provide a greater level of traceability to customers who require it on different assemblies,” commented Mario Sciberras, President & CEO of Saline. “Overall, implementing the system was an easy decision for me because of the holistic, factory-wide benefits it provides to our manufacturing team. I am very encouraged by the advanced level of data collection and process control that we will receive by utilizing TTC.”
The traceability system at Saline is currently running on 2 Juki hi-speed surface mount lines, 5 automated optical inspection machines, repair cells, as well as hand assembly and test stations. At each location the TTC System tracks every component that is used on a circuit board assembly. Tracked by the unique serial number on each PCB assembly, this system records every component required for a product including the PCBA plus each individual electronic component. In addition, the system is tracking the operator at each process station, how much time spent at each cell, and the actual work performed.
Prior to implementing this system, Saline was able to offer traceability per job lot. Now with all of this new data being tracked by Cogiscan, Saline can provide customers in the TTC Program with more granular data – including traceability to the reference designator. This will be key for many of Saline’s clients in the Medical and Aerospace markets as they typically require rigorous traceability efforts.
Product Traceability Reports
For customers enrolled in the Cogiscan Program, Product Traceability Reports detail each part number, the lot number utilized and the exact reference designator placement of each part number for the tracked assembly.
Post SMT Operations, the Product Traceability Report shows a time-stamped summary of all remaining manufacturing operations including exact cell locations. This report also provides access to the test & inspection results, and lot code traceability data for the manually added components.
Beyond showing component traceability to the reference designator, Saline can now offer real-time information by providing WIP reports. When driving for a spike demand, these new reports will give Saline’s customers an actual snapshot of an assembly’s progress through the manufacturing plant thus allowing them to provide real updates to their end users. These real-time WIP reports also display operational Yield data to help the production team recognize and react to corrective action requirements immediately.
In addition to providing real-time data, this new TTC System allows Saline to enforce a more thorough check and balance system with alerts in order to help prevent human error. Utilizing RFID Smart Feeder technology within the SMT equipment, Saline now supports automated and closed-loop validation of machine set-up and replenishment. These built-in alerts at SMT will notify operators when a reel is close to running out, or when the incorrect reel is loaded. If an incorrect reel does get loaded, the system will actually stop the line from running thus preventing any wrong parts from being placed on the circuit board assembly.
The above snapshot from the Cogiscan system shows the operators visibility of all SMT lines. The yellow square on SMT Line 1 is the built-in alarm system that notifies an operator of a reel running low.
Beyond SMT, the Cogiscan system will also help correctly route an assembly through the plant. If a product is flagged at AOI for a repair, and it mistakenly gets routed to another cell the receiving operator will get an alert to send the board back to repair in order to clear the defect originally found at AOI. These built-in alerts not only offer a way to help prevent human error in the manufacturing process, but also provide an additional quality verification to circuit board assemblies on the TTC Program.
Overall, this TTC System introduces a new level of accountability into the contract manufacturing equation. It is an excellent tool for clients to accurately measure product flow by their chosen EMS provider. By implementing this new system, Saline is demonstrating a new level of transparency seldom seen in this industry, and further strengthening the partnership with each customer. Furthermore, Saline is proving to its client base that they are prepared to take on more challenging assembly projects, and also employing rigorous methods to ensure accountability for that process.
“This project exemplifies Saline’s dedication to providing the highest-quality products at the lowest possible cost for their customers. Cogiscan’s TTC system will help Saline achieve optimal use of materials and resources throughout the entire manufacturing process, while verifying that products are assembled correctly and collecting the traceability data to prove it. These capabilities are essential to thriving in today’s economy and will help to fuel Saline’s continued growth and success,” commented Vincent Dubois, Co-President of Cogiscan.
Customers that choose to enroll in the TTC Program will gain complete visibility of their product through Saline’s production floor. Beyond the Medical and Aerospace markets, this can be extremely beneficial for clients looking to gain detailed access and quality control of an outsourced assembly. The data provided by this TTC System showcases a deeper understanding of a product’s true lifecycle opening up for potential cost reductions. In addition, this system can improve risk management in the event of a product recall as Saline will be able to provide detailed information to the specific serial numbers rather than recalling an entire job lot. This targeted recall system can save clients tenfold in money, resources and time.
As an EMS provider committed to providing real-time manufacturing solutions to customers, Saline is looking forward to the holistic improvement this TTC System will provide to its manufacturing facility. The additional data provided by this system will improve assembly processes beyond those on the Cogiscan program. Contributing to lean and sustainable initiatives, this system will help eliminate additional waste and unnecessary procedures. Wasted time on the production floor will be dramatically reduced due to the transition from manual data logging to automated RFID and semi-automatic bar code scanning. Overall, analyzing calculated through-put compared to actual real-time data will also encourage improvements factory-wide that will lead to lower costs and tighter process controls.
Since implementing the TTC System in April 2014, Saline has already seen a reduction in cycle time as the automated offline set-up validation has accelerated changeover at SMT. For Kanban and Kit Management, the built-in low level alarms are maximizing asset utilization and productivity by prompting operators to pull parts before running empty and shutting down a line. These immediate benefits will not only allow for improvements within Saline’s facility, but will also be directly felt by all clients partnered with Saline for their assembly production.
“We are very excited to roll out the Cogiscan traceability software across all of our manufacturing processes. This TTC System, working in conjunction with Juki’s Intelligent Feeder System, will provide an advanced level of control across the SMT assembly process,” commented Eric Hassen, General Manager and VP at Saline. “I’m also looking forward to the paperless method of defect data mining, which will provide quick identification of any negative quality trends that will allow us to react much sooner.”
Staying on the forefront of the changing requirements in the electronics manufacturing industry — including new regulation, smaller components, and RoHS initiatives — allows Saline to remain a competitive force in domestic contract manufacturing. Committed to giving customers sustainable and meaningful solutions, this partnership with Cogiscan provides Saline’s clients with the most innovative and advanced traceability system available.
For more information about Saline Lectronics, contact Davina McDonnell, Director of Marketing, at Saline Lectronics, Inc., 710 North Maple Road, Saline, MI 48176; 951-294-7594; E-mail: ; Web site: www.lectronics.net . For more information about Cogiscan Inc., contact Mitch DeCaire, Sales Manager, at 28-B Airport Blvd., Bromont, Québec, J2L 1S6; 450-578-1644; E-mail: ; Web site: www.cogiscan.com.
Skyscraper 1
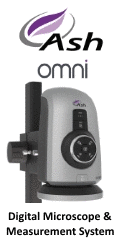