Roy Akber, CEO, RUSH PCB
The ever-increasing use of high-power LEDs for lighting and power electronics is driving the expanding use of Metal Clad Printed Circuit Boards (MCPCBs). MCPCBs offer better thermal management (dissipation) from heat-generating SMT components such as LEDs than do ordinary epoxy/glass FR-4 substrate materials. MCPCBs are typically supplied with a metal sheet as a backing for the PCB, which also provides mechanical strength. The metal sheet is usually economical aluminum, although copper may be used in special cases.
At Rush PCB Inc., we specialize in aluminum MCPCBs, available typically in three types; these are Single-Sided, Double-Sided with one side SMT, and Double-Sided.
Single-Sided Aluminum MCPCBs
Single-sided aluminum MCPCBs are the most common. These are regular PCBs with copper traces on one side of a classic FR-4 board. The reverse side of the FR-4 board bonds to an aluminum plate via a thermally-conducting epoxy. Since the thermal conductivity of standard substrates without improvements, such as FR-4, is normally low, single-sided aluminum FR-4 PCBs are not suitable for use with high-power electronics.
Double-Sided Aluminum PCB One Side SMD
For improved heat conduction, thin double-sided FR-4 material with plated-through holes (PTH) or thermal vias ensure a thermal path through the FR-4 substrate. Typically, this type of PCB has a thickness in the range 0.3 mm to 1.0 mm. The vias form the main conductors of heat, significantly increasing the vertical thermal resistance of the FR-4 material. In turn, the thermal conduction capability of the vias themselves depends on the thickness of the barrels, diameter of the via, and the via pitch. Although the standard barrel thickness is usually 2-25 µm, greater wall plating thicknesses are also used. Generally, thicker copper barrels do improve the thermal performance, but at increased cost.
It’s a common misconception that filling via holes with thermally-conductive silver paste improves the thermal conductivity of the PCB, but we find that to be only marginally true, while at the same time increasing costs significantly. Instead, our engineers have found that slightly enlarging the copper thickness of the via barrels offers better thermal conductivity performance as well as better economy. Thus, it is better to fill the vias with epoxy and cap them with copper. This has the additional advantage of placing vias directly under the connecting solderable pads of electronic components such as LEDs, resulting in direct conduction of heat. Additionally, the copper plugging prevents solder wicking or voiding during reflow soldering.
Since one side of the PCB will be bonded to the aluminum sheet, only the other side is available for mounting SMDs. Therefore, although the PCB has copper traces on both its sides, only one side is available to the designer to place SMT components. The designer is free to design the copper surface on the aluminum side to be as large as possible to achieve sufficient heat distribution across the FR-4. The level of thermal resistance depends on the number and position of vias. Thus, designing higher densities of them to be located close to the source of heat will provide better heat dissipation through lowered thermal resistance.
Double-Sided Aluminum MCPCBs
At Rush PCB Inc., we also build double-sided aluminum PCBs. The technical term for this type of PCB is Insulated Metal Substrate, or IMS. A thin dielectric or prepreg separates the aluminum support plate from the copper traces of the circuit. Although we use aluminum as the common choice for the carrier material, since it is less expensive, some customers prefer copper instead because it offers higher power densities and superior thermal conductivity. We also use metal core substrates from Univaco, Arlon, Bergquist, and Thermagon.
The layer of dielectric exerts significant influence on the total thermal performance of the IMS and governs thermal resistance. The thickness of the prepreg and its nature of bonding to the aluminum core are also critical. We use prepreg thin enough to transfer heat effectively, yet thick enough to insulate the copper conductors electrically.
The bonding process of the dielectric is very important. Air bubbles trapped between the metal substrate and the prepreg can inhibit heat transfer, since air is a poor conductor of heat. Our specialized process does not allow insulating air bubbles to remain trapped.
Direct Thermal Path for Transferring Heat
We commonly use vias for conducting heat away from hot semiconductors to the aluminum substrate through the prepreg, however this process may not be adequate for all applications. For high-power LEDs, the junction usually runs very hot and heat removal by vias is inadequate, resulting in the LED overshooting its temperature limit. This may result in premature failure of the LED unless its driver has a feedback governed by temperature, and thus can reduce the current drive to the LED. Otherwise, although the LED is saved from destruction, the performance is below expectations, and efficiency is poor.
We can improve the heat transfer rate of our MCPCBs dramatically by creating a Direct Thermal Path from the LED chip to the base metal. In a regular laminated MCPCB, an adhesive with low Tg glues the different layers together, adding thermal resistance to the overall stackup.
In MCPCBs with Direct Thermal Path, the aluminum substrate rises through the dielectric directly under the LED chip. In place of the usual thin layer of dielectric, the top of the raised part of the metal substrate has a thermally conductive layer separating the metal from the base of the LED. Since the metal substrate is practically in contact with the LED, the thermal resistance is reduced by nearly six times when compared to a traditional MCPCB.
Using Direct Thermal Path in MCPCBs makes them superior in heat removal to those using PTH vias. The metal base forms a convenient structure for thermal dissipation by lowering LED junction temperature, and provides a larger surface contact area for attaching an external heat sink.
ROY AKBER is chief executive officer of Rush PCB Inc., a printed circuit design, fabrication and assembly company (rushpcb.com); .
Contact the author at Rush PCB Inc.,
2149-20 O’Toole Ave, San Jose, CA 95131, U.S.A
Tel. +408-496-6013, www.rushpcb.com
Views
Skyscraper 1
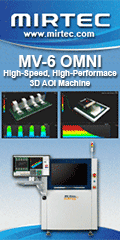