Phil Kinner, Global Business and Technical Director of Electrolube’s Conformal Coatings Division
From your perspective, how has the automotive electronics industry evolved over the past decade, and what major changes have you witnessed?
The automotive electronics industry has evolved rapidly during the last decade. The most striking aspect is the way that the use of electronic controls, sensors, safety features and in-cabin entertainment, communications and navigation, have been adopted in mid and low-end vehicles. Automobiles are now much safer, more fuel-efficient and more comfortable as a direct result of the increased adoption of electronics.
On top of this, we have seen the emergence of electric vehicles offering a more environmentally acceptable alternative to fossil-fuel based vehicles. These electric vehicles now have a range that is useful to most commuters and we are seeing a rapid installation of charging stations and other infrastructure requirements to make these vehicles more mainstream.
Finally, we’ve seen the emergence of smart cars that can communicate with each other, making pre-emptive interventions to help maintain safety and avoid collisions, with ‘driverless’ vehicles making daily journeys on highways and other roads without major incident. Who would have thought that would be close to a practical possibility a decade ago?
From an industry standpoint, the challenge today is to build reliable electronic products with increasing density, complexity and sophistication while at the same time, meeting the many automotive regulatory requirements. Please give your comments here. Where does Electrolube come in to help automotive electronics customers achieve this?
I would say that the challenges on electronics reliability in the automotive industry are perhaps higher even than aerospace applications, due to the fact that aerospace systems usually have at least 2 back-up systems that automotive systems do not. The elimination of cleaning from many automotive electronics assembly processes has placed an even greater emphasis on the performance requirements of the protective coatings.
Given the volume of automotive parts produced, the use of solvent-containing products is discouraged to help meet solvent-emissions targets. The list of prohibited substances for use in automotive applications continues to grow. The manufacturing processes need to be ‘lean’ and provide ‘one piece flow’ at the maximum possible, defect-free, manufacturing velocity.
Electrolube recently received the International Automotive Task Force’s new global quality management standard, IATF 16949, and as an ISO14000 company, we are dedicated to producing products that can help automotive manufacturers achieve all of their requirements, whether it is the demonstrably higher performance solvent-free conformal coatings, encapsulation resins for more demanding applications, high performance lubricants and greases for enhancing switches, bearings and other moving parts or advanced thermal management for keeping assemblies cool to extend their lifetimes, Electrolube has a great portfolio of products to help enhance the reliability and productivity of automotive electronics.
As a conformal coatings provider, what are the main challenges that you encounter from your customers in the automotive electronics space?
We see our customers needing to achieve ever higher operating temperatures as the electronics continue to become more powerful resulting in higher temperatures, also, historically electronics have been considered in-cabin or under-hood, with greater requirements for under-hood applications. We are seeing a blurring within these boundaries and a drive towards using one material in both applications to simplify manufacturing processes.
From a performance point of view, thermal shock, the rapid transition from extremely cold, towards maximum operating temperatures, originally intended as a destructive test methodology has become an important acceptance criteria for customers, with the number of cycles increasing from 1000 towards 2000. This poses real challenges for some solvent-free chemistries, especially UV curable materials, so popular because of their manufacturing attractiveness from a ‘lean’ and ‘one piece flow’ point of view.
Balancing the requirements of environmental acceptability, manufacturing acceptability and end-product reliability continues to be the main challenge facing coating formulators and Electrolube has recently introduced a new range of conformal coatings at Productronica 2017 to help users address all of these issues simultaneously.
Are there different types of conformal coatings suited to automotive electronics? Please highlight some of the best practices that help automotive electronics makers select the correct conformal coating solution for their applications.
There are many types of conformal coating that may be suitable for automotive electronics from Acrylics, Urethanes and Silicones that have been used historically, through to modern UV curable hybrids and even ‘ultra-thin’ coatings. The correct choice will always be dictated by a combination of performance requirements, manufacturing requirements and environmental considerations.
From a performance requirement point of view, the manufacturer must consider the end operating environment and determine likely minimum and maximum operating temperatures, consider the likelihood of splash or immersion in water or liquid spills, humidity/condensation and chemical exposures e.g. salt-spray, corrosive gases or unintentional oil spills etc.
From an environmental point of view, the use of solvents needs to be considered, along with other chemicals that may be banned by company policy or international regulations such as RoHS, REACH etc.
Finally, the manufacturer must give consideration to the possible coating application methods that may be used to manufacture the assembly and assess likely impacts on manufacturing throughputs, floor space requirements, Work In Process (WIP) and manufacturing velocity. They must also ensure that their application process and material selection work together to give an acceptably defect free process that meets their end reliability requirements.
Considering these 3 key areas together, a manufacturer may find that a material that performs well in all 3 consideration factors, may be more suitable for their purposes than a material that has excellent environmental characteristics, but does not suit their manufacturing processes.
What new advances are available for conformal coatings?
Electrolube has developed a new range of innovative VOC-free, fast-curing, high performance two-part conformal coatings designed for application by selective coating, which can be easily adapted to a selective coating system with a simple two-part feed modification. The fundamental chemistry behind Electrolube’s new ‘2K’ coating materials is not new, but the 2K, solvent-free selective coating process is a new and enabling technological breakthrough, that allows all the benefits of 2K coating materials to be realised.
The 2K materials provide a solvent-free alternative to both UV and silicone materials, requiring less capital investment than UV materials and improving on the performance of most silicones in harsh environments. We have subjected the new 2K range amongst UV and silicone coatings to scrutinising tests, which included thermal shock, powered salt-spray, condensation and mixed flowing gas (MFG) testing. New 2K products include the 2K350, 2K850 and 2K550 polyurethane coatings. 2K350 is a UL94V-0 compliant, solvent-free coating which is opaque blue for ease of inspection and has an operating range of -40 to +130°C. The hydrophobic coating gives excellent water immersion, salt mist and humidity protection, making it an excellent choice for automotive electronics. The new 2K550 is a tough, flexible, high performance coating with a UV trace, which is also a UL94V-0 compliant coating and is characterised by greater coating thickness and enhanced edge coverage. The 2K850 features all the benefits of the 2K system, with the speed and convenience of UV cure, enabling an immediate tack-free coating, whilst ensuring rapid and reliable secondary curing in areas shadowed from exposure to UV. The 2K850 system also has a wide operating temperature range of -40 to +130°C with excellent thermal shock performance.
Has the increase in automotive electronics had an effect on your business? If yes, please explain.
Apart from the increased fiscal benefits, the main effect has been the requirement to implement more robust systems and procedures, to ensure we can make a quality product precisely, consistently, efficiently and safely, to provide our customers the level of confidence they require from their suppliers. Year on year, our automotive clients raise the bar with their expectations from both a manufacturing perspective, but perhaps just as importantly from a product development point of view. At Electrolube, we are consistently driven to produce products that solve the ever-increasing challenges in process and performance issues faced by our customers. We are constantly innovating new solutions to meet the rapid advances in electronics manufacturing, which is the foundation of our culture and our success.
What qualifications are required for your company to get on an automaker’s accredited vendor’s list?
It is necessary to have a strong quality management system, but more than that, to have an attitude towards continuous improvement and minimizing defects and errors. This needs to be part of the company culture and a willingness to supplement the quality framework, with additional tools and procedures to satisfy the particular requirements of the automotive manufacturers. It is more an attitude towards quality then blindly following the procedures.
Automotive electronics manufacturers are looking for a partnership rather than the traditional buyer/seller relationship, and the more flexible and open to implement different ideas we can be as a supplier, the more we can earn the trust of our partners.
With this confidence, we come to understand our customer’s problems better, and understand what we can do to solve these problems. Delivering elegant solutions to known (and sometimes unknown or unacknowledged) issues adds further value to the partnership, completing a virtuous cycle.
The automotive industry, to my knowledge, only has several OEM published specifications relating to material performance requirements, with many others requiring compliance with IPC-CC-830. Testing our products to above and beyond these minimum requirements, ensures that our customers can be confident in both the quality and performance of these materials, and have confidence that the materials selected can withstand their expensive qualification testing.
What do you see as the biggest driver of automotive electronics innovation, i.e., safety, reliability, efficiency, etc.?
I think all those factors will continue to drive the development of electronics innovation in the automotive industry. Historically, efficiency was the initial driver, with the development of fuel injection systems. As our fossil fuel reserves continue to dwindle, and gas prices continue to rise, there seems little reason to think that consumers won’t demand more fuel efficient vehicles, or that these developments would not be considered a key part of corporate social responsibility amongst the automotive manufacturers.
Safety was the next driver, with the development of systems such as air bags and anti-lock brakes, but the development work on self-driving cars is likely to only raise the bar on safety requirements, and this will go hand in hand with ever increasing reliability requirements since this will be a key component of the self-driving car philosophy.
With our ‘always connected’ lifestyles, and the advent of the ‘smart home’, the ‘smart car’ is the logical next step, and this will require new electronics and new ruggedisation techniques to ensure the electronics continue to work flawlessly.
What is your outlook for the automotive electronics industry, from the perspective of a conformal coatings provider?
The unique reliability challenges provided by automotive electronics will continue to drive the development of new chemistries and new processes to provide ruggedisation to the electronics systems. Conformal coating will continue to be a key part of that ruggedisation tool kit, although perhaps not in exactly the same form as we are used to. Electrolube will continue to play a key role at the forefront of these innovations.
There is no doubt that solvent-emissions will become more closely regulated at some point in the future, so I expect low and zero-VOC coating materials to become the new normal. I expect the performance requirements of ruggedised electronics to become ever more demanding, requiring the very highest performance protection possible. With the ‘do more with less’ philosophy inherent in society, I also expect the need for higher yield conformal coating processes, with faster cycle times, greater manufacturing velocities and greater levels of automation to become commonplace.
Views
Skyscraper 1
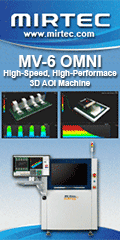