By Don Lockard with support from Vince Parente, Manufacturing Engineer, & Nick Siciliano, Manufacturing Engineering Manager
In the world of volume electronics manufacturing, seconds count. Cycle time is the rate that manufacturing printed circuit board (PCB) assemblies complete the manufacturing process on an assembly line. The world’s most productive PCB assembly plants produce PCBs or panels of PCBs at cycle times of less than 20 seconds. Plants run 24/7 and there is urgency in how the factories are managed. Recognition that any time the production equipment is not producing PCBs, money is being lost. In the science of economics, this is called “opportunity cost.”
The United States produced most of the PCB assemblies in the world until the exodus of the industry offshore in the early 1990s. Now many plants in the United States, using the same equipment and more expensive labor than their overseas competitors, produce little. Equipment sits idle for most of the day, awaiting all the necessary tasks to be accomplished to make it run. When something happens that stops the line, it is accepted as part of the process, and corrected in a casual manner. It is a grand waste of capital and labor, and contributes significantly to our manufacturing un-competitiveness in the world.
Industry in the United States largely manufactures those PCB assemblies that are not allowed to be produced overseas, such as military electronics equipment or fast turn assemblies used in product development. Neither of these activities requires PCB producers to compete anywhere near world market pricing. The result is an industry with expectations from its capital investments that are not on the same playing field as their overseas competitors.

Lenze Americas’ engineering team outside the company’s facility in Uxbridge. A leading manufacturer of AC drives, the Lenze Americas is modernizing its manufacturing process to become as productive and efficient as possible.
Lenze Americas is a manufacturer of AC drives in the cradle of the American Industrial Revolution: Uxbridge, Massachusetts. Lenze has a high product mix of more than 400 assemblies. The Lenze manufacturing engineering department undertook an effort to modernize their production. Their goal is to become a much more productive manufacturer. To achieve this, a throughput with cycle times as low as 20 seconds and an OEE rate (overall equipment effectiveness) of over 80 percent are targeted. These are lofty goals in this high-mix facility.
In order to accomplish this, Lenze partnered with Samsung, a company that knows how to produce a competitive product and one of the leading producers of PCB assembly equipment in the world. Samsung won the competition for the job against other leading equipment producers because of its speed, flexibility, value, and customer support. The new production line would be the first step in a phased replacement of an existing four SMT line plant of equipment.
The placement rates of the Samsung equipment could handle the speeds necessary to make the throughput rate and cycle times of 20-60 seconds. The challenge was to accomplish this on a line, 115 ft long (including through-hole placement and wave soldering). At any one time there can be as many as 50 boards in process, and there also can be more than one product on the line. Lot sizes can be as small as two PCB assemblies. Production must take place in what Lenze calls a “rolling changeover.”

Lenze Americas’ engineering team chose to partner with Samsung because of the speed, flexibility, and value of its equipment. The new production line is the first step in a phased replacement of an existing four SMT line plant of equipment.
A “rolling changeover” requires line operators to make all changes (from the stencil to the components to all the equipment programs) in such a small amount of time that it does not significantly interfere with the production rates. The plan is to have each piece of equipment change programs automatically. Once product “A” is produced, product “B” may be produced as a PCB passes a scanner at the entrance of the each machine. This will be accomplished from the destacker to the printer and on down the line. A requirement is that the PCBs must be identified with a bar code. Lenze found the most economical way to accomplish this is to have a laser marker make an unremovable mark. As each board is processed, equipment programs change automatically for SPI, three Samsung placement machines, reflow oven, AOI, and full nitrogen tunnel wave soldering.
Every change of tooling and set of components unique to each PCB must be in place as the board passes through – a tall task. In order to accomplish this, everything has to be planned carefully. Lenze is planning to use a MES software program called iTAC to accomplish this, but the most challenging part is having the thousands of electronic components ready on new feeder carts in place. Samsung management software, TOLP (total offline production) is perfect for planning and executing this task. The Samsung management software package allows production to be planned beforehand, not only maximizing the production efficiency of the placement machines, but also minimizing the work to changeover to each unique product. The setups are accomplished offline to optimize productivity.
The biggest challenge in accomplishing this improvement is training the personnel that are required to carry out the job. In order to illustrate the challenge, Lenze incorporated in their training an interactive Lego game that simulates lean production, moreover a film showing an Indianapolis 500 pit crew operating in 1952 and comparing it to one from 2013. The change is stark and so is what is required of Lenze’s manufacturing employees. Every movement in today’s pit crew is reviewed to remove seconds. The same is being employed at Lenze; everything is checked so that it is ready beforehand and when the change occurs, the team snaps into action. It will take a while to get it where it will be, but it is moving in the right direction.
The benefits to Lenze Americas as of this writing are impressive. To start, “Production Time” (the time to complete an assembly from raw material to a finished product) has been reduced by 76 percent. Lead times on their product have been reduced by 19 days. Four SMT lines have been reduced to three. The team has confidence that the changes make Lenze a more competitive company in its marketplace. Plans to continue this effort are already under way.
For more information about Lenze Americas, contact Susan Duval, Marketing Manager, at . Visit www.Lenze.com for more information. To find out more about SAMSUNG C&T Automation, Inc., contact Don Lockard at Yankee Soldering, , 401-965-3812 or visit www.samsungsmt.com.
Skyscraper 1
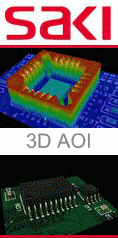