By Tom MItchell, North American Business Manager, Conecsus LLC
Sanmina, one of the world’s leading contract manufacturers and EMS companies, is recognized in around the world as a ‘green’ company, and one that uses state of the art processing for waste treatment. But their high-volume, high technology PCB manufacturing facility in Huntsville, Alabama, which produces advanced electronic products for some of the world’s leading medical and defense companies, also produces a significant volume of hazardous metals waste. Sanmina produces state of the art PCBAs (Printed Circuit Board Assemblies) on several advanced SMT (Surface Mount Technology) lines. Many of these SMT lines produce products in high volumes, and thus Sanmina is classified as a “Large Waste Generator”. For SMT, the primary by-products are solder dross and solder-contaminated consumables. Responsibly managing and disposing of these materials was costing the facility between $12K – 20K per year, depending on manufacturing volumes. One of the agencies Sanmina works with to certify processes and procedures for hazardous waste disposal is the Alabama Department of Environmental Management, or ADEM, one of the strictest state regulatory agencies in the country.
“We tried a total of three times over the years to get ADEM to approve different processes for dealing with this waste that we advanced,” says Patsy Smolik, CMfgT, Regional Environmental Health and Safety Engineer at the Sanmina Corporation facility. “Twice they turned us down, because the process that we suggested, while efficiently dealing with the waste, was not ‘true’ recycling of the material. They were very strict about that.” Sanmina always met or exceeded environmental standards for waste treatment, but was always looking for a better, greener way that would cost less. And wasn’t there a way, somewhere, to recycle this material?
The stakes were huge; Sanmina provides advanced technology products to some of the world’s most innovative companies. These products have electronics using lead and lead-free solders depending on the application. There is considerable diversity in the waste streams, and as regulations continue to tighten, the costs associated with dealing with hazardous waste continue to rise.
In 2014, the facility shipped 12,000 pounds of waste material for processing and disposal. That’s a lot of dross and solder-contaminated consumables. There had to be a more efficient and environmentally friendly way of processing these materials.
The solution was developed in 2013 by Conecsus LLC, and is known by the acronym RACS (Reducing Agent: Coke Substitute). This technology process is focused solely on the waste stream colloquially known as “contaminated trash”. This material is generally comprised of under-stencil wipes, spent paste, tubes and jars, gloves, rags, finger cots, and other similar items that are, from a regulatory standpoint, a characteristically hazardous and regulated waste. Toxic metal residues are what cause this material to be considered hazardous by regulatory agencies, and these cannot be processed or transported in the same fashion as solder dross when a generator has a “Small or Large Quantity Generator” status. As such, they are very expensive to manage or dispose of, and a great deal of record keeping is required to remain compliant with state and federal regulations. The RACS technology allows Conecsus to take that material and re-use it as a reagent ingredient in the processing of other materials, such as solder dross, filter cakes, detinning dross, and other tin or lead residues. This small but important distinction in many cases gives generators in most states the ability to ship it to Conecsus with the dross on a common carrier, with a bill of lading along with their solder dross. This may eliminate the need for an expensive hazardous waste carrier, or processing the material through a hazardous waste management firm.
“Dealing with metal residues and metal contaminated residues from Surface Mount Operations, can be expensive and complex” explains Steve Burns, Regional Sales Manager for Conecsus LLC. “When we initially approached Sanmina with our RACS solution, they were very skeptical, and understandably so. They had already tried twice to get ADEM to approve more progressive solutions for dealing with contaminated surface mount residues and trash. With our system, contaminated waste becomes a useful product, a reagent in an industrial process that produces a product with value.
“We had to get approval from the regulatory staff at ADEM before Sanmina would approve of the new process RACS provides,” Steve continues. “If managed as hazardous waste by environmental companies, these materials normally go to fuel blending or landfill. Hazardous waste minimization and sustainability are goals of many responsible companies like Sanmina. Additional cost savings are realized in the fact that, when these materials are shipped to Conecsus, they can be shipped common carrier. When classified as hazardous waste, higher-priced regulated carriers are required.”
The patented Conecsus RACS technology allows generators to send their solder-contaminated waste to Conecsus as a reagent replacement rather than as a hazardous waste, and as a result, it also reduces the amount of hazardous waste that the client generates because they no longer have to report these materials as hazardous waste. The RACS process allows the refiner to re-use the carbon units, containing metallics, as a reagent in Conecsus’ other pyrometallurgical processes, and this reduces the amount of coal products needed for their reagent values in refining impure metals. RACS material is up to 30% more effective than the coal products in reducing oxidation in impure metals. This further reduces the purchase of coal products while simultaneously reducing the amount of carbon dioxide that is released from the refining process where RACS is used. In short, it will lower a generator’s carbon footprint as well as lower their reportable waste streams, both of which are a significant benefits from an environmental as well as financial perspective.
Gregory Bryant, Facility EHS for the Huntsville Facility, say that “Working with this new process changed everything. We no longer had to ship our materials as before at great cost; instead, they (Conecsus) send a truck to pick it up. We pay a nominal processing fee. Sanmina receives payment for the metals in return, that is often significantly greater than the original processing costs. The most important thing is that we are reusing, not disposing. It’s not only in keeping with Sanmina’s ‘green’ objectives, but it changes the way that Sanmina may be classified or regulated. We have to maintain our “Large Waste Generator” classification due to the multiple waste streams that we produce. But in our medical operations for example, fully 98% of the wipes we dispose of are now non-hazardous solid waste, recycled by pyrolizing and then used as a reagent to process our dross.”
Greg says that this year alone (2015), up until the end of March, up to 1,500 lbs. of waste had been shipped, with a savings of thousands of dollars in hazardous material processing charges. “It has saved us a tremendous amount of money,” he adds. “Conecsus refines the material and sells the metals on the global market. They don’t return it to us; they simply pay us for it. The wipes and contaminated materials don’t generate metals of any value, their value is in being turned to carbon and used as a reagent to recover the metals in our dross; that’s really where the money comes from.” And all of this is done with the approval of ADEM, something that they never thought they would obtain.
Views
Skyscraper 1
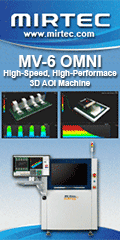